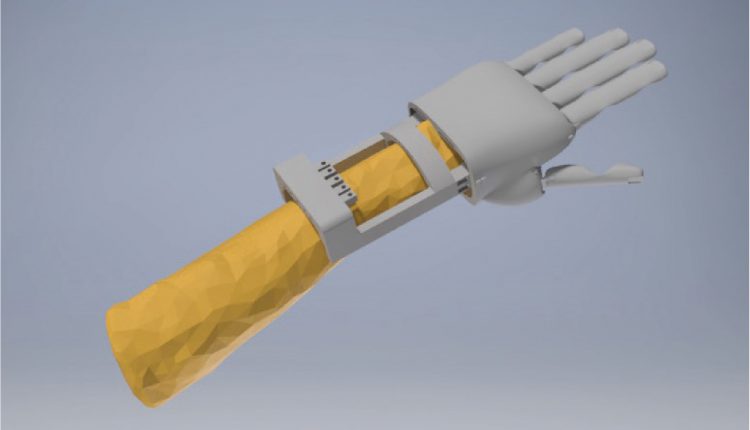
Use of 3D printing in the manufacture of prosthetic hands
Uso de la impresión 3D en la fabricación de prótesis de mano
Christian Pérez Fernández (1) , María del Mar Espinosa (2) , Manuel Domínguez (3)
Abstract
3D printing is very popular in society, mostly due to fused deposition modelling, allowing prototypes and products of varying degrees of reliability to be created quickly and easily. In the case of hand prostheses, where the existence of high-cost commercial designs is inaccessible to a large percentage of the population, this technology is shown to be an alternative to the manufacture of this type of device at a much lower cost. This article gives a brief introduction to additive manufacturing technology and the development of the different types of hand prostheses that can be found. Examples of mechanical and myoelectric prostheses are shown, in which different types of mechanisms and functionalities common to the vast majority of designs that people develop in universities, research centres, NGOs or as independent volunteers can be seen.
Keywords: Prosthetic hands, 3D printing, prosthesis.
Resumen
La impresión 3D posee una gran acogida en la sociedad, debido en su mayoría al modelado por deposición fundida, permitiendo crear prototipos y productos de una mayor o menor fiabilidad de forma rápida y sencilla. En el caso del campo de las prótesis de mano, donde la existencia de diseños comerciales de alto coste económico inaccesibles para un gran porcentaje de la población, esta tecnología se muestra como una alternativa a la fabricación de este tipo de dispositivos con un coste muy inferior. En este artículo se realiza una breve introducción a la tecnología de fabricación aditiva y al desarrollo de los diferentes tipos de prótesis de mano que pueden encontrarse, mostrando ejemplos de prótesis mecánicas y mioeléctricas, en los que pueden comprobarse diferentes tipos de mecanismos y funcionalidades comunes en la gran mayoría de diseños que distintas personas desarrollan en universidades, centros de investigación, ONGs o como voluntarios independientes.
Palabras clave: Manos protésicas, prótesis de mano, impresión 3D, prótesis
Received 06/09/2021 Accepted 03/01/2023
1-3 Design Engineering. Universidad Nacional de Educación a Distancia (UNED). Juan del Rosal, 12. 28040 Madrid, Spain
Corresponding author: Christian Pérez Fernández, cperez1522@alumno.uned.es
Introduction
Thanks to the development and accessibility of 3D printing in recent years, not only in industrial and educational environments, but also in domestic environments, society has become more involved in the creation of designs to be manufactured using this type of technology, achieving a wider range of possibilities and examples of useful elements for society. In this aspect, the field of prostheses for people with loss or absence of upper limbs has been impacted, as in this case, hand prostheses, which have had several developments thanks to the cheapness and easy adaptability that allows the use of 3D printers, allowing access to this type of technology for a much lower price than proprietary designs, something important in the case of developing populations or in the case of young people of growing age, in which it would be necessary to change prostheses successively until they reach adulthood.
Material and methods
The method used for the research and writing of the article is theoretical, having carried out a search for information related to the topic to be developed in a general way for the two areas it covers.
In order to carry out the process, scientific articles and reference bibliography have been sought through:
– IEEE Xplore.
– ProQuest Research Library.
– Google Scholar.
The keywords used in the searches are: prosthetic hands, 3D printing, and prosthesis.
Searches were carried out only in Spanish and English in the different media mentioned above, selecting articles and documents in which different examples of designs and developments of prosthetic hands using 3D printing technologies could be seen.
3D printing
3D printing has existed in our society for more than 30 years. In recent years, thanks to the expansion of more affordable 3D printers, such as those based on fused deposition modelling (FDM), together with other movements such as open source. This is based on sharing technical knowledge, encouraging participation between the different people who can take part in its development, both in software development and in plans and threedimensional models, as in this case.
An example of this is the RepRap movement (Koprnický & Šafka, 2017), whose name comes from the basic idea of replicating itself, i.e., creating 3D printers that can print parts to make other printers. This fact allows us to understand the fabrication of prostheses using this technology, in which it is normal to share designs to help people in need, using the idea of self-replication (Dally, et al., 2015).
3D printing concept
3D printing is a type of additive manufacturing based on the superimposition of successive layers of material in order to obtain a threedimensional object or part (Fernández, 2016). It can be considered slower compared to mass production if the aim is to produce a large number of products (Koprnický & Šafka, 2017), but in the case of the manufacture of prototypes, as well as the production of unique or customised items, it becomes a more efficient and optimal process due to the use of less expensive materials and means, both energy and machinery (Fig. 1).
It also allows the production of unique or customised items, being able to create complicated, geometries or non-standardised parts of various sizes with good aesthetic and functional properties in a more cost-effective way (Mohammadi, et al., 2020).
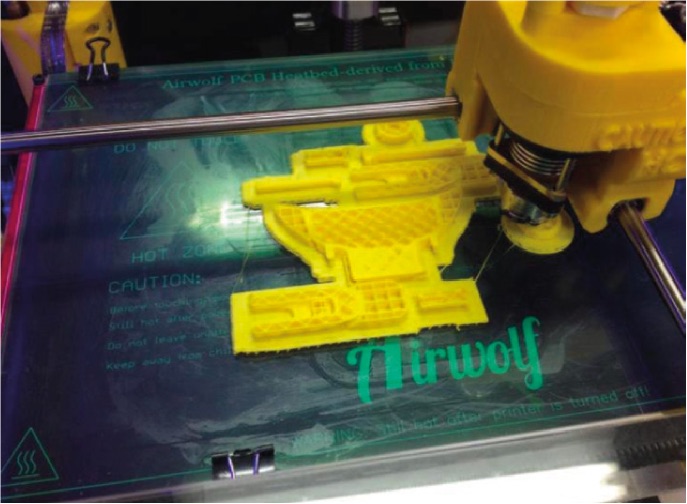
Printing technologies
Different additive manufacturing technologies have been developed but, because of its wide use in the production of this type of prosthesis, only the following types will be discussed:
– Stereolithography: Stereolithography (SLA) is an additive manufacturing process in which the photopolymerisation of resins, i.e., liquid polymers, is used to manufacture three-dimensional objects or models. An ultraviolet laser travels across the surface of the material in the XY planes, solidifying the parts needed to obtain the geometry of the solid body. When the layer of the material solidifies, the platform on which the resin is located descends, making it easier for the beam to work on the following layer of the solid, repeating the process successively until the three-dimensional element is obtained (Fernández, 2016). Post-treatments in ovens are often used to improve the mechanical properties of the model.
– Fused deposition modelling: This type of technology uses spools of filament that pass through an extruder at temperatures, depending on the type of material used, of around 200 °C. Heating the filament reduces its diameter to the order of microns, while the extruder follows the appropriate trajectory to generate the layers of the three- dimensional model. This extruder can move along the XYZ axes, with the base on which the material is deposited being fixed (an example can be seen in Fig. 1), or it can move along the XY axes, with the base being movable along the Z axis, similar to the stereolithography process (Fernández, 2016). This type of 3D printing is the most widely used in the manufacture of prostheses, due to the wide variety of printers and their cost, which is considerably lower than that of other technologies, together with the voluntary nature of the group of individuals who own this type of machine (Sánchez & Falfán, 2019), who are dedicated to designing or manufacturing prostheses for people who can use them. The spools used in this process can be found in different filament diameters, around 3 mm, and there is a wide variety of materials, with two being the most commonly used:
•ABS: acrylonitrile butadiene styrene is an amorphous thermoplastic terpolymer with high impact resistance often used in the automotive industry, e.g., in the manufacture of bumpers. Each of its three monomers provides different characteristics: acrylonitrile provides rigidity, resistance to chemical attack, hardness and stability at high temperatures; butadiene provides toughness at low temperatures and impact resistance; while styrene, similar to the previous ones, provides mechanical strength, hardness and rigidity.
•PLA: polylactic acid is a thermoplastic derived from the starch of vegetables such as maize or cassava. It is biodegradable and decomposes slowly in contact with water and carbon oxides. It is denser than ABS and harder, but with less elasticity and resistance to impact and high temperatures. There are types of filaments that use different materials to achieve different looks and properties, many of these are based on adding additives to the PLA or ABS itself, such as spools made from nylon, polystyrene or flexible materials.

Prosthetic hands
The hands, limbs located at the limit of the upper extremities, are the main tool for physical manipulation of the environment by human beings, thanks to the two primary capabilities they have: pressure and touch; allowing the performance of movements, grasping and holding objects, as well as their sensitive qualities (Fernández, 2016) (Loaiza & Arzola, 2011).
Gripping ability is largely due to the thumb, which has the power to rotate 90 degrees (Brito, et al., 2013), which, together with the remaining four fingers, gives the hand the ability to mould and adapt to the shape of the objects or surfaces with which it interacts (Castellanos, et al., 2011) (Fig. 2).
Due to the events of World War II, more than 20,000 people had limbs amputated; 120,000 civilians were amputated as a result of disease or accidents (Rodríguez & Saldaña, 2018). Amputations or malformations can affect patients both psychologically and socially, in addition to the economic cost to their quality of life, due to the search for prosthetic solutions or the impossibility of carrying out work or trades.
The manufacture of prosthetic hands seeks to fulfil two fundamental objectives: on the one hand, functionality, giving the opportunity to recover the movements and capacity to hold, use and interact with objects and the environment; on the other hand, aesthetics, by recovering the symmetry between limbs and the standard appearance of the human body, solving conditions derived from malformations or amputations.
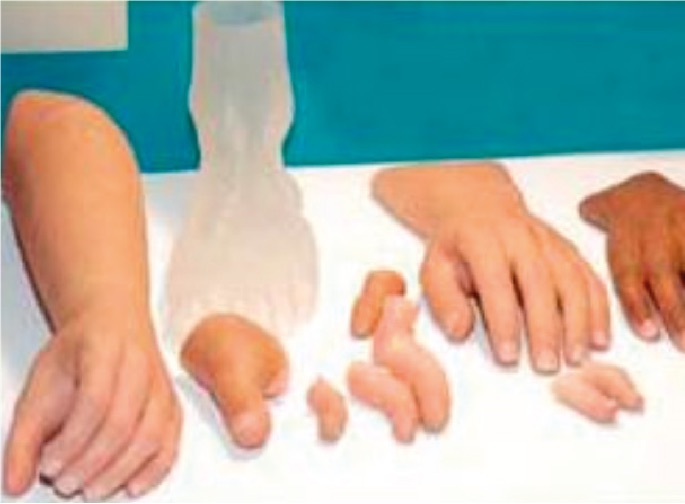
Evolution of prosthetic hands
The development of prostheses has gone hand in hand with the development of materials, technologies and knowledge of the human body (Fig. 3).
Prostheses appear as early as the civilisations B.C. (before Christ), as well as in the medieval times. Most of these prostheses had an aesthetic rather than a functional function.
Amputation of limbs in battle was common. It could be said that the prostheses of those times had a secondary functional function, such as holding the shield of soldiers in order to use the sword with the hand they still possessed (Fernández, 2016).
During the 20th century, with the advent of the World Wars and after the Civil War in the USA, the great innovations in prosthetics took place, as the aim was to enable amputees to return to work once their military service was over.
In 1912, Dorrance developed the Hook prosthesis, which could be opened and closed by the movement of the scapula with the aid of a harness. Later, in 1946, pneumatic and electric active prostheses were developed. It was in Russia in the 1960s where the first myoelectric type active prosthesis was produced. This prothesis used sensors in the muscle mass of the amputated limb stump in order to effect the movement of the hand/ gripper (Fernández, 2016).
With the technological advances of the time, numerous hands or upper limb prostheses were developed and appeared, which were designed with a focus on robotic tasks. However, lighter hand models were also developed, such as the Otto Bock hand (Brito, et al., 2013), which has the main advantage of being able to grasp objects quickly and precisely in an active manner thanks to the sensors in the fingers (Fig. 4).
With the arrival of the 80s, the hand of Scottish origin ProDIGITS appears, presented for different types of amputation or absence of limbs of the upper extremity, being improved in 1994, achieving an improvement in the size of the mechanisms and power source (Castellanos, et al., 2011).
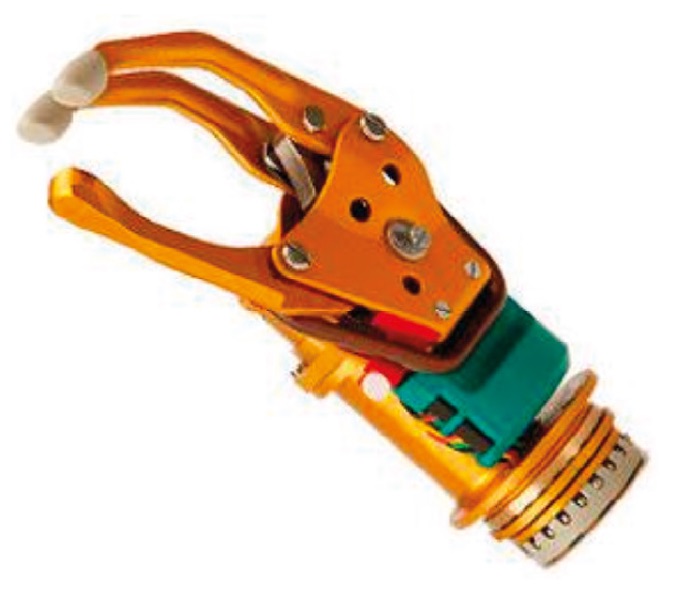
In the following image (Fig. 5) you can see the first design, compared to a later one.
In recent years, the development of new technologies together with the improvement of the lives of people with missing or amputated limbs, as well as competition between companies, has led to a great evolution in this field, achieving improvements in precision and in the number of movements and orientations, with a wide range of models and updates of older versions appearing. One example is the creation of artificial skins that mimic the touch of a human hand; this is related to myoelectric prostheses, seeking a mind-machine connection, where commands and movements are more natural and instantaneous.
One example is the I-Limb prosthesis, in which each of its fingers is controlled independently, facilitating a large number of positions with precision thanks to a 90 degree rotation of the thumb (Brito, et al., 2013) (Fig. 6).
Classification of active prostheses
Active prostheses are those that do not merely fulfil an aesthetic function but can carry out tasks due to the mobility and control of their different parts by the individual. According to their mode of action, they can be classified as follows.
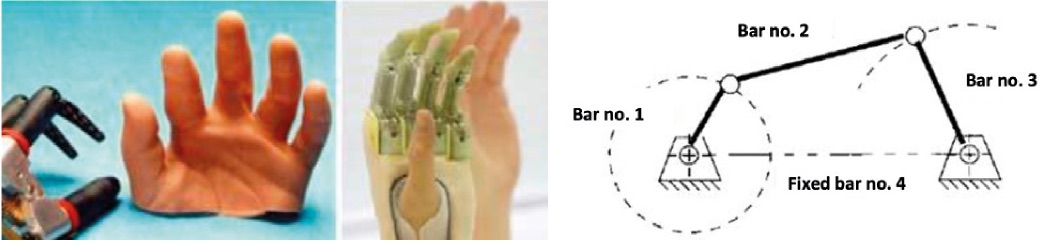
Mechanical prostheses
Mechanical hand prostheses are devices that, in most cases, facilitate a grasping or clamping action, i.e., they can be closed and opened to hold or grasp objects. They are usually controlled by harnesses or cables attached around the wrists, shoulders, chest, etc. They are not very precise. One of the mechanisms used for the operation of some mechanical prostheses is the so-called articulated quadrilateral or four-bar mechanism, shown in figure 7. In this mechanism, three of the bars are mobile and one is fixed, one bar generates the movement and the other receives it, with the movement of one being rotational on its axis, while the other performs a see-saw movement; the movements can change, with both being rotational or seesaw. Grashof’s Law (Eq. 1) is used to check Figure 7. Articulated quadrilateral (Castellanos, et al., 2011). the type of motion.
In which:
S = length of the shortest link,
L = length of the longest link,
P and Q = length of the remaining links.
This type of mechanism, with design and execution possibilities of greater or lesser complexity, can be used, for example, for the operation of prosthetic fingers, managing to imitate the movement of the phalanges. Other types of mechanism used for the operation of this type of prosthesis is the use of springs for the flexion or extension of the limbs (fingers or hooks/hooks) accompanied by tensors, cables or bars, which carry out the opposite operation to the spring, i.e. if, thanks to the tension of the cables, the hand closes, when these are relaxed, the springs would return the hand to an open position, and vice versa (Fernández, 2016). An example can be seen in the following pictures with a Snap-Together prosthesis design from Robohand, where in the first case the fingers are at rest (Fig. 8), while in the second picture it can be seen that when the wrist part is flexed, the fingers close thanks to the use of tensioners (Fig. 9). The majority of 3D printed prostheses are of this type, due to the simplicity of the mechanisms, as they use the user’s own movements or strength and do not have electronic elements.
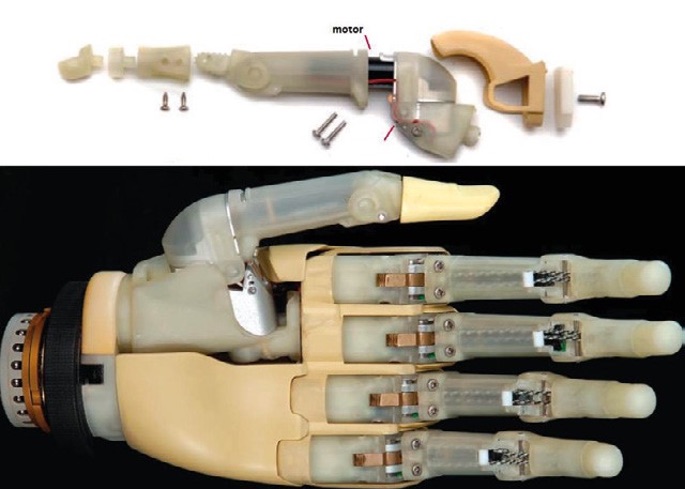
Electric prostheses
Electric prostheses are powered by electric motors, replacing the force of the user and the type of mechanisms used in the previous example mentioned. They are controlled by a push button or switch with a harness operated in a similar way to the mechanical ones.
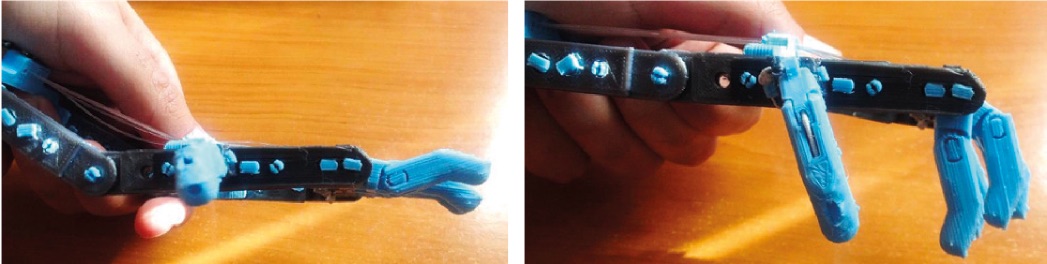
Pneumatic prostheses
The first designs of pneumatic prostheses were powered by the use of compressed carbonic acid, but due to the complications and risk they could cause to the user, their manufacture and development has been abandoned.
Currently, pressurised air obtained by means of a compressor is used, allowing great strength and speed in movements (Brito, et al., 2013), although it is costly to maintain due to the complexity of its mechanisms and the use of relatively large devices.
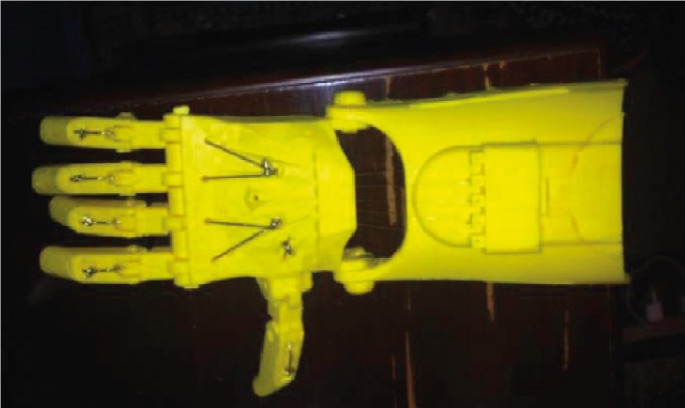
Myoelectric prostheses
Myoelectric prostheses are the most developed type at present. They combine the action of the body by means of myoelectric sensors located on the periphery of the amputated area. These elements pick up small electrical signals originating from the nerve endings and muscles of the individual’s organ or residual limb, transmitting them to one or more microcontrollers, which translate them into commands for the actuators that govern the various movements of the prosthesis.
There are surfaces electrodes, placed on the skin, and electrodes inserted inside the individual’s tissue. Two types of hand-integrated sensors can also be found:
•Position sensors: these are used to measure the position of the fingers and joints, an example being the socalled Hall sensors, accompanied by magnets, to measure the movement and angular position of the element.
•Force sensors: these are used to measure the force that is being applied to the prosthetic fingers when they come into contact with an object, e.g., FSR sensors (resistive force sensors).
Long-life batteries are used to power he sensors, actuators and the microcontroller circuit board, allowing the device to operate for at least one full day (Fernández, 2016). One such example could be seen in Figure 6.
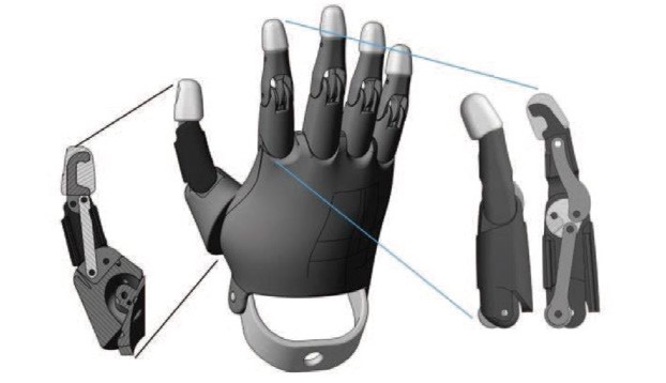
3D printed prostheses
As mentioned, most 3D printed prostheses are mechanical, employing mostly the same type of mechanism, using wrist flexion to achieve finger closure.
An example is the Raptor Hand designed by R. Borjas and W. Flores (Fig. 10). The Raptor Hand model consists of an assembled set whose fingers are elevated 25 degrees by means of ropes that generate a permanent tension in the resting state of the hand, forcing it to open. When a change of angle is generated, the tension is increased, acting so that the hand finally executes the flexion of the fingers (Borjas & Flores, 2015).
This type of design is very useful in developing countries due to the low cost of its manufacture compared to commercial models, as well as its use focused on growing children, being able to successively print different sizes for the following stages until maturity, thus saving the use of commercial prostheses for each of these phases.
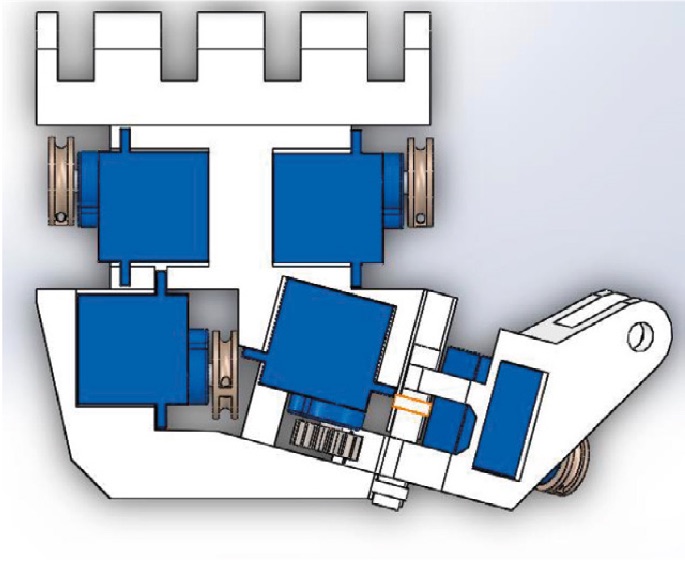
In the prosthesis developed by Marlene Bustamante’s team (Bustamante, et al., 2018) a parameterised model of a prosthetic hand was devised, which could be successively scaled up using the measurements of the patient’s other healthy hand, carrying out a 3D scan of the residual limb in order to design a comfortable cavity for its use.
In order to carry out the parameterisation, different sections or measurements of the palm and fingers were marked, seeking a proportionate configuration and scaling.
On the other hand, a complementary software for AutodeskTM Inventor was developed to help insert and change the parameters of the 3D model and customise the prosthesis in an intuitive way. With the previous study of the lengths of the hand segments, the formulas for their parameterisation were included in two parts of the software: an Excel file and a program developed in the Visual Studio development environment using the AutodeskTM Inventor application programming interface (API). The former performs the calculations and transfers the necessary dimensions to the design program; the latter receives the calculations and updates the parametric design via buttons on a user interface before proceeding to export the files for 3D printing (Bustamante, et al., 2018).
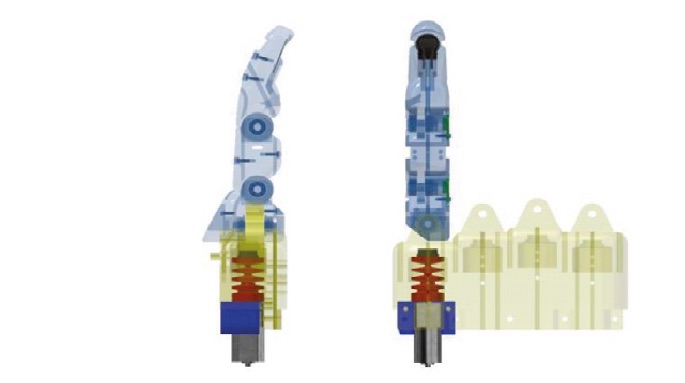
The design of the fingers consists of three four-bar links, the length of each link was calculated according to the Grashof equations and the anthropometry of each user, i.e., the length of each finger. The positions of the joints are aligned with the axes of rotation axes of the fingers (Fig. 11).
The activation or flexion of the fingers is achieved by means of tensioning cables as in other mechanical prostheses, with the difference that, in this case, the cable pulls on the handle of the first four-bar joint. This movement produces the rotation of the following phalanges by their crank links.
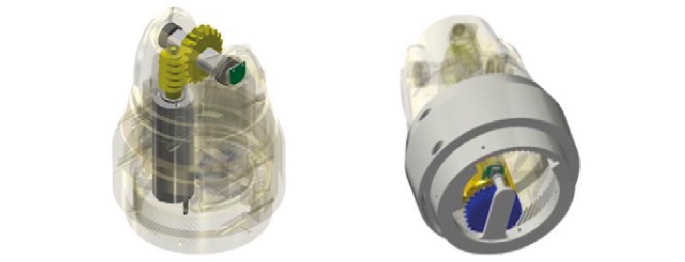
With regard to the development of myoelectric prostheses, there has been an increase in the number of developments, thanks to open-source microprocessors such as Arduino, being able to easily program and control the different actuators and components of the hand, while it is possible to manufacture cavities and housings for the different elements in a simple way with the additive manufacturing techniques already mentioned.
A prosthesis of this format and low cost is the one presented by Víctor Ferman, Carlos de la Cruz and Ali Lemus (Ferman, et al., 2015), called Galileo Hand, in which its distribution is intended as a kit available for potential users to make their own model.
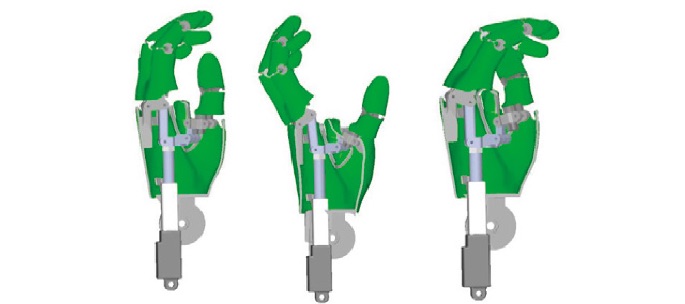
It has 5 small servomotors that transfer movement to the parts that make up the hand (Fig. 12). The fingers are made up of three phalanges and the thumb is able to rotate, allowing the whole assembly to be moulded more easily to the object or surface with which it is intended to interact. Elastics are used to force the fingers open, forcing them to return to rest, using the actuators simply to close the fingers or rotate the thumb.
A more complete myoelectric prosthesis in terms of the possibility of movement and degrees of freedom is the one designed by Victoria E. Abarca’s team (Abarca, et al., 2019), Octa Hand. This prosthesis has an active wrist that allows turning on itself to change the orientation of the hand and six types of grip thanks to the configuration of its fingers: rest, tip, tripod, powerful, spherical, and extension.
The mechanism includes four cables per finger, two for each phalanx and a pulley (Fig. 13). Each pulley works with two sides, one taut and one loose, when the pulley moves to the right the finger executes the flexion movement and when the pulley moves to the left the finger executes the extension movement.
The wrist has two degrees of freedom, its flexion/extension movement is carried out by a worm gear from 0 to 70 degrees. In addition, it includes a self-locking system to the movement of the axis and joints of the hand. Pronation movement from 0 to 90 degrees and supination movement from 0 to -90 degrees is carried out by an internal worm gear (Fig. 14). Each degree of freedom of the hand must have an angular position sensor that measures the absolute position. Its main advantage is that no initial position calibration is required when the prosthesis is turned on in any position. It has eight compact actuators that work independently to meet the necessary torque and speed requirements. As discussed above, part of the function of prostheses is aesthetics, so it is important to design realistic prostheses that simulate the skin and properties of the human body. The team of Masahiro Yoshikawa (Yoshikawa, et al., 2015) presents the Rehand, a myoelectric prosthetic hand (Fig. 15).
It consists of a hand, a support bracket and a control box that includes an operating system using a distance sensor. The gripping function is achieved by a simple linkage mechanism with an actuator. The opening and closing of the fingers are controlled by changes in the distance between the distance sensor and the skin surface caused by the bulging of the muscle during muscle contraction.
The joints of the thumb and other fingers are actuated by the simple linkage mechanism that works with the extension of the linear actuator shaft simultaneously.
The fingers open and close according to the extension of the linear actuator shaft and proportional to the user’s level of muscle contraction.
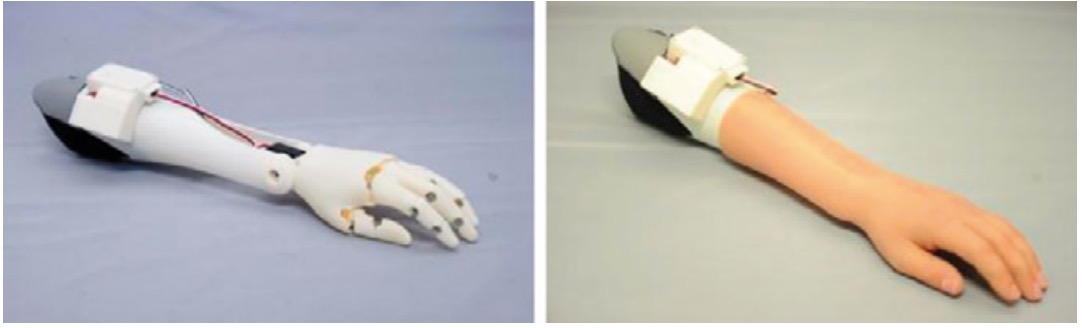
The entire prosthesis is covered with a commercial glove that adheres to the prosthesis thanks to its shape and design, giving a more natural look and concealing the 3D printed mechanism and parts (Fig. 16).
Conclusions
The expansion of 3D printing, making it a more accessible technology for society to the point where additive manufacturing machines are now available even at home, has led to the emergence of an increase in three-dimensional designs and models related to various fields.
In this case, the development of prostheses to be manufactured with this technology, from mechanical to myoelectric, by research centres, universities, NGOs or independent volunteers, makes it possible to create an alternative at a much lower cost than the possibilities of commercial brands, not always within the reach of the entire spectrum of the population.
The opportunity for customisation and scaling, as in the case of children who have to change prostheses year after year due to their growth, is one of the clear examples of the value of this manufacturing alternative.
This type of device, together with the aforementioned open source, becomes a global solution in which users or interested parties can carry out specific modifications, as well as the creation of new designs based the mechanisms or functionalities shared by others.
To sum up, the union of 3D printing and the design of prostheses is a field in continuous development, bringing on hope to a large part of the world’s population that cannot access to other models of higher range and price.
It is undoubtedly worth mentioning the use of this technology to create study prototypes that can later generate final products to be manufactured with other types of processes and more resistant materials, seeking to produce more durable and reliable products.
References
Abarca, V. E., Flores, K. M. & Elías, D., 2019. The Octa Hand: An Affordable Multi- Grasping 3D-Printed Robotic Prosthesis for. Beijing, China, s.n.
Borjas, R. & Flores, W., 2015. Developing a Human Prosthesis using a 3D printer in Honduras. Panama, s.n.
Brito, J. L., Quinde, M. X., Cusco, D. & Calle, J. I., 2013. Estudio del estado del arte de las prótesis de mano. Ingenius. Revista de Ciencia y Tecnología, Enero-Junio(9), pp. 57- 64.
Bustamante, M., Vega-Centeno, R., Sánchez, M. & Mio, R., 2018. A parametric 3D- printed body-powered hand prosthesis based on the fourbar linkage. Taichung, Taiwan, s.n.
Castellanos, C. A. S. et al., 2011. Diseño mecánico y cosmético de una prótesis parcial de mano. Revista Cubana de Investigaciones Biomédicas, 30(1), pp. 15-41.
Dally, C. et al., 2015. Characteristics of a 3D-Printed Prosthetic Hand for Use in Developing Countries. Seattle, WA, USA, s.n.
Ferman, V., Cruz, C. d. l. & Lemus, A., 2015. Galileo Hand: Diseño de una prótesis biónica subactuada de bajo costo utilizando impresión 3D. El Salvador, s.n. Fernández, C. P., 2016. Diseño y fabricación de mano protésica mediante impresión 3D. Gijón: Escuela Politécnica de Ingeniería de Gijón.
Koprnický, J. & Šafka, J., 2017. 3D printed bionic prosthetic hands. Donosti-San Sebastian, s.n.
Loaiza, J. L. & Arzola, N., 2011. Evolución y tendencias en el desarrollo de prótesis de mano. DYNA: revista de la Facultad de Minas. Universidad Nacional de Colombia, 78(169), pp. 191-200.
Mohammadi, A. et al., 2020. A Paediatric 3D-Printed Soft Robotic Hand Prosthesis for Children with Upper Limb Loss. Montreal, QC, Canada, s.n.
Rodríguez, V. A. & Saldaña, J. J., 2018. Prótesis en impresiones 3D de bajo costo “Hand To Hand”. Chiriquí, Panamá, s.n.
Sánchez, E. J. A. & Falfán, L. G., 2019. El impacto de la impresión 3D en la construcción de una prótesis de mano. Publicación Semestral Pädi, 7(Especial), p. 27–31.
Yoshikawa, M. et al., 2015. Rehand: Realistic Electric Prosthetic Hand Created with a 3D Printer. Milan, Italy, s.n.