Herramientas para la resolución de problemas dentro del “Total Performance Management” (TPM)*
Total Performance Management” Problem Solving Tools (TPM-PST)
Resumen
El Lean Manufacturing en todo su conjunto, o el Total Performance Management (TPM) en específico, constituyen la base de los sistemas de producción modernos muy vinculados a la tecnología 4.0 tanto de moda en nuestros días. Este artículo presenta los fundamentos de dos sistemas de resolución de problemas, bien en la modalidad de problema sencillo y cotidiano que no necesita toma de datos ni herramientas de tratamiento estadístico (GSTD), o bien su vertiente más compleja con herramientas avanzadas (DMAIC). Estas herramientas son uno de los pilares que permiten a las empresas mejorar sus resultados, además de otras muchas herramientas como la gestión de indicadores, reuniones operacionales, plan maestro operacional, estándares de limpieza, inspección y lubricación, estándares de centerlining y cambio rápido de formato (SMED).
Palabras clave: TPM, Lean Manufacturing, resolución de problemas, GSTD, DMAIC.
Abstract
Lean Manufacturing as a whole, or Total Performance Management (TPM) in specific as a part, constitute the basis of modern production systems, closely linked to 4.0 technology. This article introduces the basics of two problems solving tools, either in the easy and everyday problem solving way that does not require data storage or statistical processing tools (Go-See-ThinkDo) or either if the problem is more complex, it requires advanced tools (Do-Measure-Analyse-Implement-Control). These two tools are one of the pillars that allow companies to improve their results in addition to many other tools such as indicator management, operational meetings, operational master plan, cleaning, inspection and lubrication standards, centerlining standards, and rapid format change tool (SMED).
Keywords: TPM, Lean Manufacturing, Problem Solving, GSTD, DMAIC.
Recibido / received: 08/04/2019. Aceptado / accepted: 28/04/2020.
* CODIGO UNESCO: 531109 Organización de la producción
1. Emilio José García Vílchez. Ingeniero técnico industrial en Química, ingeniero en Organización Industrial y doctor en Ingeniería de Procesos y Sistemas por la Universidad de Valladolid. Postgraduado en Logística e Ingeniería de la Calidad.
Autor para correspondencia: Emilio José García Vílchez E-mail: emigarvil@gmail.com
Introducción al sistema de producción de Toyota
El sistema de producción de Toyota (TPS) (Fig. 1) constituye el sistema productivo más implantado y con mejores resultados. Como la mayoría, surge a partir de la necesidad. Cuando la familia Toyoda decidió competir abiertamente en el sector del automóvil terminada la Segunda Guerra Mundial, se dio cuenta de que no podía hacer frente a las empresas norteamericanas que producían a bajos costes, gracias a la producción a gran escala en masa, con un gran despliegue de medios técnicos y fuertes inversiones, y sin cambiar de formato, dado que se producía básicamente un modelo de coche y en un único color.
El ejemplo más claro de esta industria era Ford, que fabricaba una gran cantidad de automóviles en serie que no se diferenciaban entre sí en nada (Ford T negro) (Hernández y Vizán, 2013). Kiichiro Toyoda, que inició la producción de automóviles en el año 1933, ni podía producir en grandes cantidades, ni disponía del enorme capital que esta industria norteamericana tenía invertido en equipamientos.
Por tanto, solo quedaba una opción para la recién nacida Toyota: conseguir la misma eficiencia produciendo pequeñas cantidades y sin grandes inversiones.
Pues bien, esto solo se conseguiría encontrando los costes improductivos del sistema a gran escala. Así es como se establecieron los principios que dieron lugar al modelo de gestión que desarrollaron y sus herramientas, por lo que se llegó a un sistema mucho más eficiente.
Además, el método destaca de este sistema la involucración de las personas como un punto indispensable de la mejora continua.
El TPS se estableció a partir del concepto de «justo a tiempo» (just in time o JIT) en el que cada proceso produce solo lo que se necesita en el siguiente. Posteriormente surgiría la revolución Lean desarrollada en la década de 1950 por esta empresa automovilística.
¿Qué lo diferencia de los demás sistemas de producción? ¿Por qué llegó a ser tan exitoso? Analizando estos 14 principios uno puede comenzar a responder estas preguntas. Para facilitar su comprensión, el autor dividió estos principios en cuatro categorías a las que denominó las “4P” porque cada una de ellas comienza con P en idioma inglés: Filosofía (Philosophy), Proceso (Process), Gente y Socios (People and Partners) y Resolución de Problemas (Problem Solving). El modelo de las 4P de J. Liker (2004) se representa gráficamente mediante una pirámide con base en la Filosofía y ascendiente hasta la Resolución de problemas. Desarrollaremos cada categoría, detallando cada uno de los principios incluidos (Fig. 2).
(I) Filosofía a largo plazo Como estamos acostumbrados, todo sistema o concepto de origen japonés constituye no solo un modo de trabajar, de hacer las cosas, sino que tiene base en una filosofía, en un modo de pensar y ver las cosas, una manera de vivir alineada con principios arraigados. Como filosofía oriental, TPS basa sus decisiones en el largo plazo, sin buscar resultados inmediatos y efímeros. Toda la organización debe estar alineada con la filosofía, y entender que no se busca únicamente el lucro.
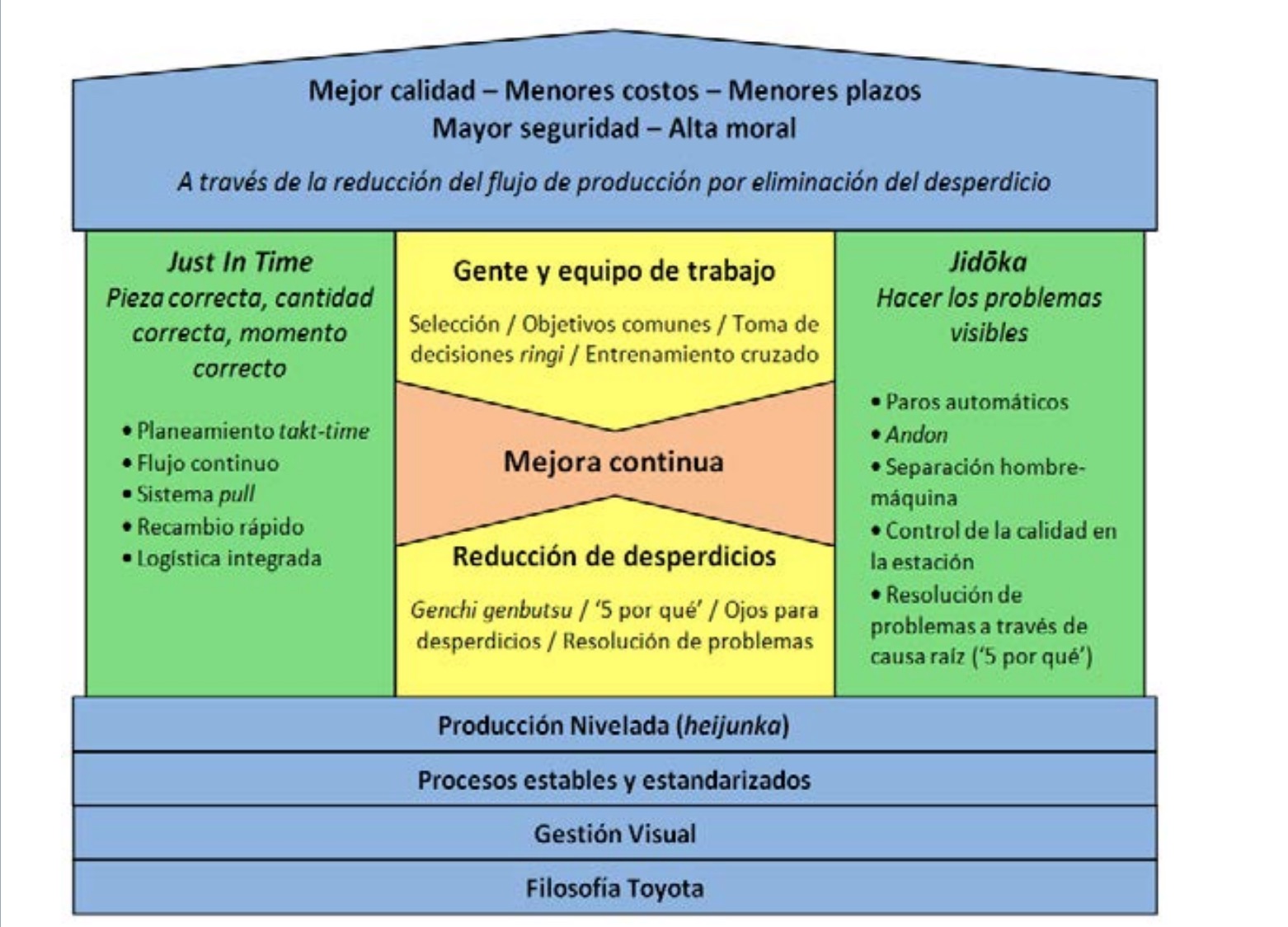
Principio 1: Basar decisiones de la dirección en filosofía de largo plazo, aun a expensas de metas financieras de corto plazo.
(II) El proceso correcto producirá los resultados correctos Esta categoría se centra en los principios fundamentales que rigen el funcionamiento del pensamiento just in time (JIT). Incluye los principios que tienen que ver con lo operativo y estratégico del sistema.
Principio 2: Crear un flujo de proceso continuo que lleve los procesos a la superficie.
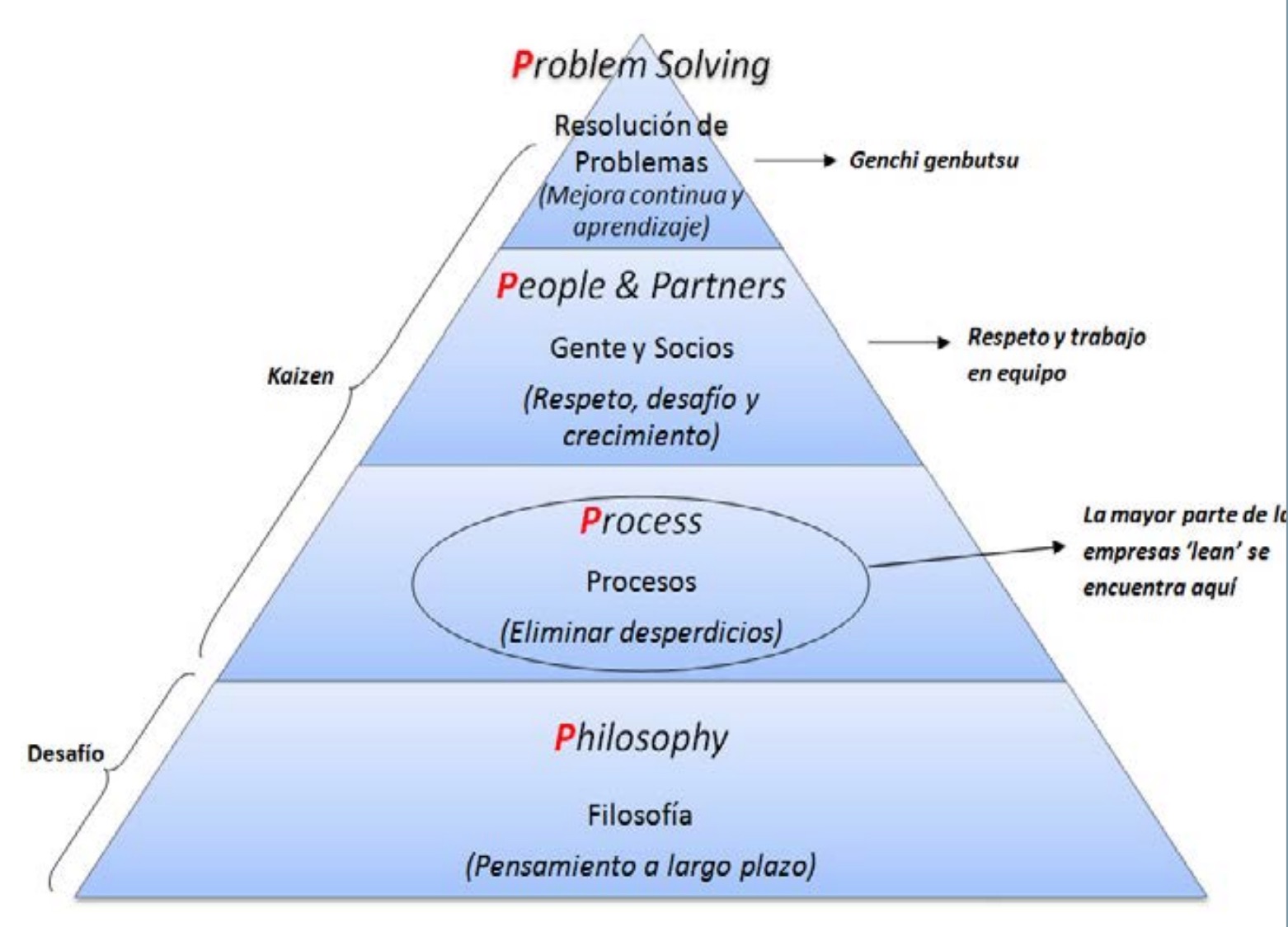
Principio 3: Usar sistemas pull para evitar la sobreproducción (se produce según la demanda, el ritmo lo marca el cliente).
Principio 4: Elevar equilibradamente la carga de trabajo (heijunka): Trabaje como una tortuga, no como liebre.
Principio 5: Construir una cultura de detener los problemas fijos, para conseguir la calidad correcta la primera vez.
Principio 6: Las tareas estandarizadas son fundamentales para la mejora continua y el empoderamiento del empleado.
Principio 7: Usar el control visual para que los problemas no se escondan.
Principio 8: Usar solo tecnología fiable, testeada exhaustivamente que sirva a los procesos y la gente.
(III) Agregar valor a la organización desarrollando a su gente y socios Los socios y proveedores conforman una red de mutua colaboración. Son propiamente una extensión del propio negocio. El grado de participación en los cambios y las mejoras es fundamental.
Principio 9: Generar líderes que entiendan profundamente el trabajo, vivan la filosofía y enseñen esto a otros.
Principio 10: Desarrollar gente excepcional y grupos que sigan la filosofía de su compañía.
Principio 11: Respetar la red extendida de socios y proveedores, desafiándolos y ayudándolos a mejorar.
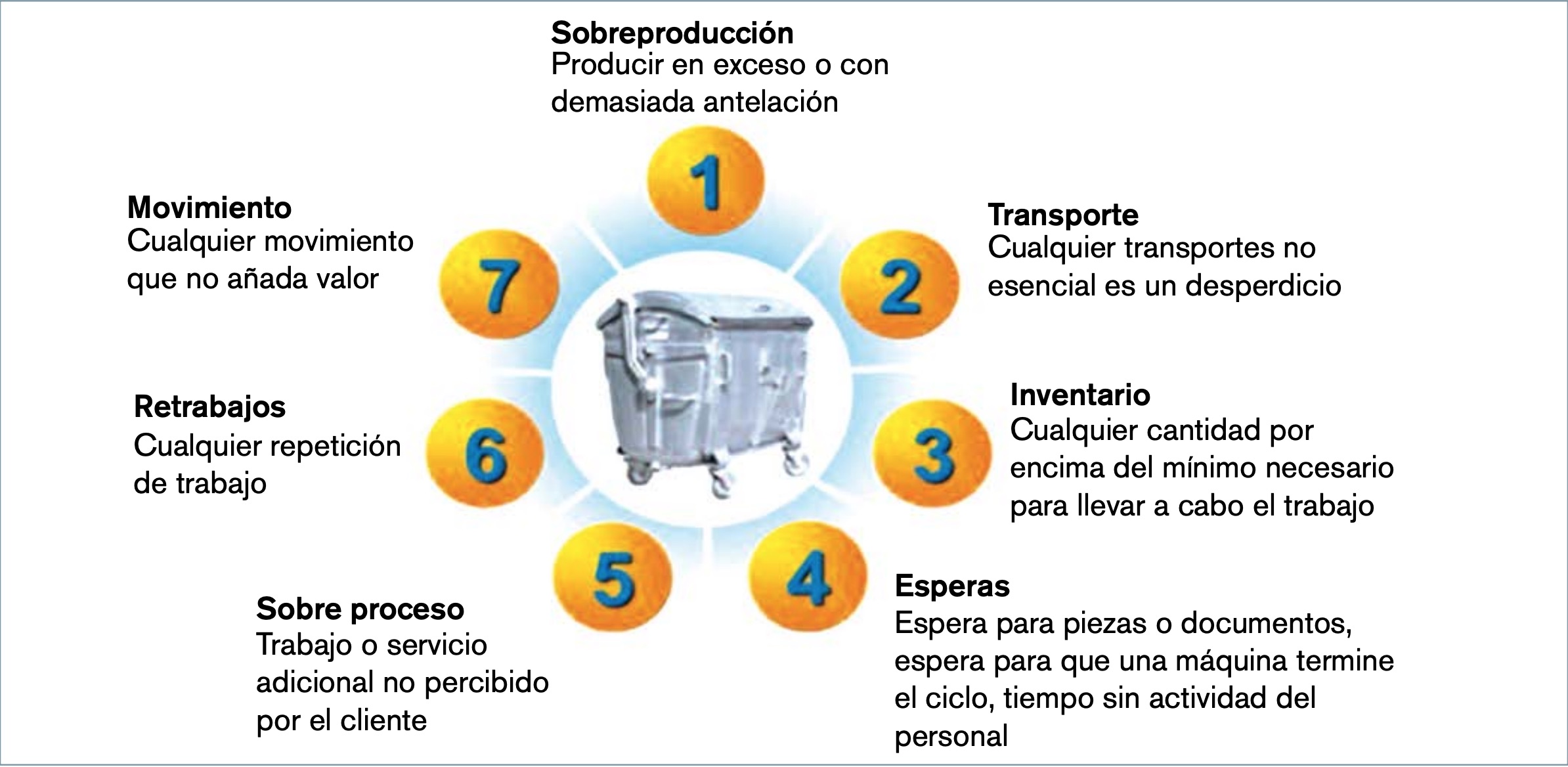
(IV) Solucionar continuamente los problemas lleva al aprendizaje organizacional Toyota posee un sistema muy particular de gestión del conocimiento denominado como genchi genbutsu, que involucra a la gente en el análisis de un problema y la invita a ver las cosas por sí misma, personalmente en el lugar real de ocurrencia (v. siguiente epígrafe). Esto evita subjetividades propias de la abstracción o de basarse en opiniones o comentarios de un tercero. También se considera la importancia de nemawashi como un método sumamente innovador de toma de decisiones basado en el consenso. Por último, dos conceptos ancestrales, que son la esencia de los sistemas de producción japoneses: la búsqueda de la mejora continua, el kaizen, y la autorreflexión, el reconocimiento y el aprendizaje de los errores: el hansei.
Hay un tema clave: cuando se detecta un problema, y hasta que se resuelve, hay que adoptar un “mientras tanto” como medida correctiva rápida para evitar que el problema pueda ir a más o causar algún daño inesperado.
Principio 12: Ir y ver por uno mismo para entender profundamente la situación (genchi genbutsu).
Principio 13: Tomar decisiones lentamente, por consenso y considerando todas las opciones detalladamente, e implementar decisiones rápidamente (nemawashi).
Principio 14: Los paros imprevistos como
principal fuente de despilfarro (hansei) y mejora continua (kaizen).
Los paros imprevistos como principal fuente de despilfarro
La eliminación de costes improductivos, aspecto que persiguen todas las empresas, dio lugar al concepto de desperdicio o despilfarro (en inglés waste, en japonés muda), es decir, consumo de recursos que no aportan valor alguno al producto y que erosionan, por tanto, el beneficio. Estos desperdicios que se tratan de evitar de acuerdo con los principios del TPM se categorizan en siete familias (Ruíz y García, 2015) (Fig. 3).
A estos siete desperdicios se le debe añadir uno más: el humano. No utilizar todo el potencial de los trabajadores es un desperdicio. La creatividad y las ideas de los trabajadores pueden ser una vía para solucionar los problemas de la fábrica, e incluso puede llegar a ser la herramienta más efectiva.
Por tanto, la cultura Lean no es algo que empiece y acabe, sino que es algo que debe tratarse como una transformación gradual y firme en el pensamiento si se pretende que sea duradera y sostenible (Liker y Meier, 2006). Los paros imprevistos suponen una de las principales fuentes de despilfarro identificadas por Toyota dentro de su sistema productivo (TPM) en las líneas de producción, ya sea por esperas o retrabajos principalmente (Ruiz y García, 2015).
A continuación, vamos a determinar cómo la generación de paros imprevistos supone el principal problema productivo de las líneas de fabricación. Indirectamente, además de la repercusión en costes que genera tener una línea de producción parada, contribuye a otros factores muy relevantes como (Liker, 2004):
– Incidentes de seguridad laboral: una línea de producción parada obliga al operario a intervenir en la máquina más veces de las necesarias. Esto puede generar, por tanto, un accidente laboral aunque solo sea por la recurrencia. Para minimizar este aspecto hay diferentes herramientas como los procedimientos para intervenir en máquina. Entre ellos destaca la consignación y bloqueo de equipos (LOTO), la seguridad basada en la conducta para trabajar el ámbito de la actitud a la hora de intervenir, el cumplimiento de las normas de acceso, etc.
– Cumplimiento de especificaciones de calidad del producto fabricado: si el proceso no es estable se generan problemas de calidad, tanto en el contenido como el en packaging, que pueden repercutir en bloqueos de producto, reclamaciones por parte del consumidor, pérdida de confianza en la marca, etc. Si tenemos un proceso continuo siempre seremos capaces de cumplir con las especificaciones técnicas definidas para nuestro producto de desde el punto de vista sensorial (color, olor, sabor, textura, etc.) y analítico.
– Servicio a clientes a tiempo y en cantidad: además, si las líneas de producción se detienen inesperadamente no seremos capaces de fabricar lo requerido y podemos no servir correctamente al cliente en tiempo, lo que supone también una pérdida de ventas que puede ocasionar una desconfianza del consumidor en la marca.
– Costes de materiales y personal: el tiempo en el que los equipos de producción están parados supone un despilfarro de materiales que hay que tirar y el coste de la mano de obra directa de las personas de la línea, lo que implica un sobrecoste que el consumidor no está dispuesto a pagar. Como no podemos repercutir este coste al cliente, supone una erosión de la cuenta de resultados.
– Gestión de los residuos generados: los residuos que se ocasionen como consecuencia de la generación de producto no conforme es necesario segregarlos con el gestor. Esto supone, además de un sobrecoste, una contribución negativa para el medio ambiente.
Por tanto, atacando los paros imprevistos seremos eficientes en todas las áreas de gestión de una organización de forma indirecta. Este debe ser el foco.
En este sentido, las herramientas para la resolución de problemas son correctivas, dado que se utilizan cuando hay un problema que está generando un despilfarro. En función de la complejidad del problema se utilizarán unas u otras.
Las herramientas para la resolución de problemas (principios 12, 13 y 14)
Las principales herramientas utilizadas para la resolución de problemas son el “ir” (go) “ver” (see), “pensar” (think) y “actuar” (do) (se suele nombrar por sus iniciales sajonas como GSTD) y los equipos de resolución de problemas DMAIC (definir, medir, analizar, implementar y controlar). Los equipos DMAIC pueden ser básicos y avanzados en función de su nivel de complejidad (la gran mayoría son básicos porque un problema complejo generalmente se secciona en varios problemas más simples interrelacionados) (Climent, 2005).
Las diferencias más importantes entre una herramienta y otra se resumen a continuación (Tabla 1).
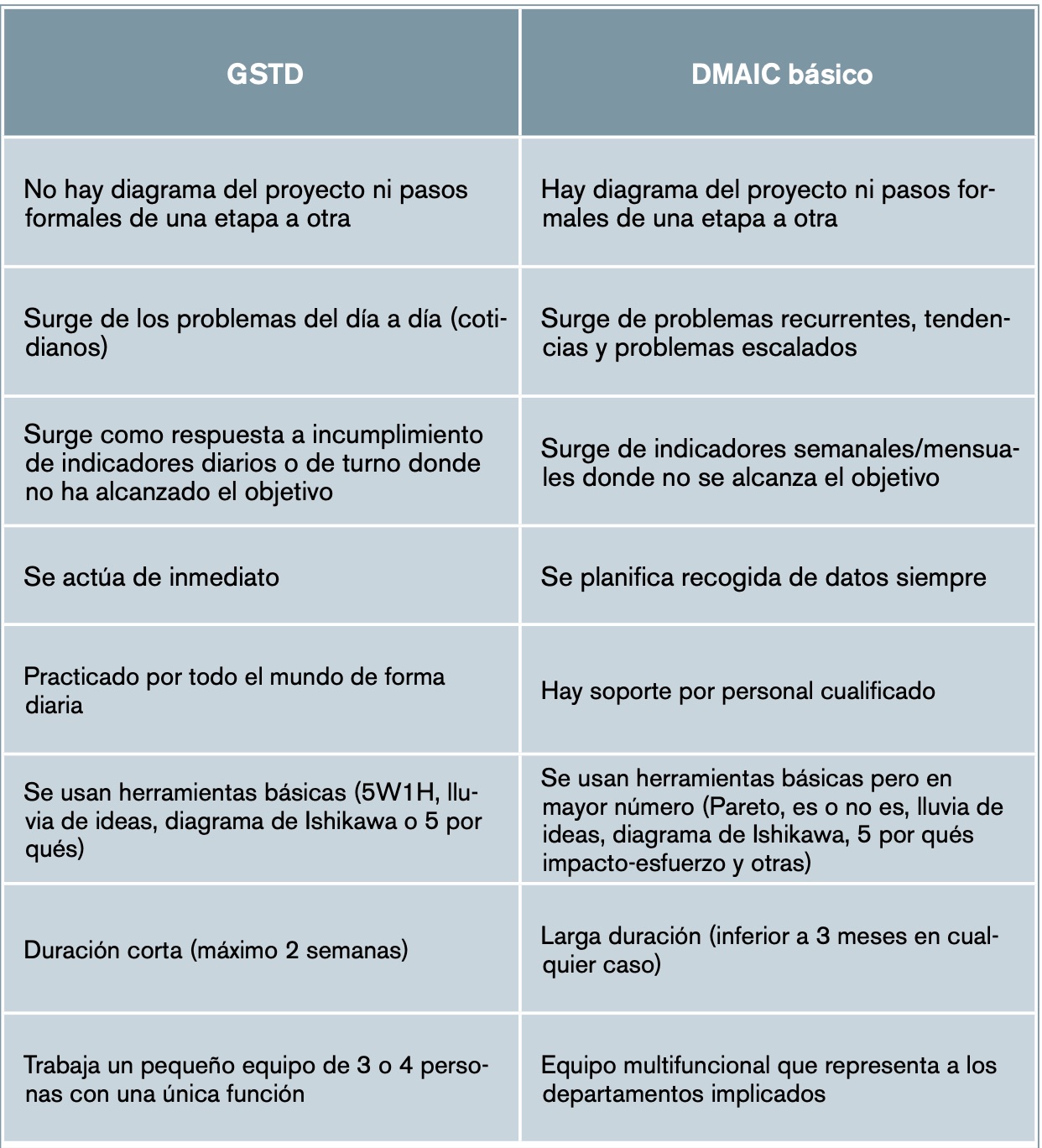
Ir, ver, pensar y actuar (GSTD)
GSTD es una herramienta que sirve para resolver problemas cotidianos (Shook, 2011). Consta de una parte de ir y ver el problema para entender qué está pasando realmente (go & see), una segunda parte de análisis de causas potenciales (think) y una última parte de actuación donde se ejecutan las acciones que van a contribuir a que el problema no se repita (do). Vale para resolver cualquier problema básico de cualquier aspecto (seguridad laboral, calidad, costes, servicio).
Las etapas iniciales de ir y ver (go & see) tratan de entender y acotar el problema para poder saber concretamente lo que está pasando y a qué indicador de gestión diario o semanal nos está afectando. Partiendo de los síntomas (lo que observamos), en este momento, además de entender lo que sucede (problema en sí mismo), hay que preguntarse si se está trabajando en condiciones normales: la máquina trabaja en condiciones básicas, los materiales están según especificación, se están siguiendo los procedimientos de trabajo y se comprueba si se siguen los procedimientos de mantenimiento. En este momento se usan las siguientes herramientas básicas: el diagrama de flujo, croquis o esquemas y el 5W1H (qué, dónde, cuándo, quién, cuál y cuánto) para sacar una definición consolidada del problema.
En la etapa de análisis (think) se hace una recopilación de las posibles causas que han podido generar el problema (a partir de la etapa anterior mediante una lluvia de ideas) para poder conocer la causa raíz que lo ha generado a partir de la lluvia de ideas, diagrama de Ishikawa y 5 por qués. Hay que verificar cada causa potencial para confirmar qué puede haber contribuido directamente a la consecución del problema.
Por último, en la etapa de actuar (do) es necesario asociar un plan de acción para cada una de las causas detectadas y, una vez ejecutadas, medir la efectividad de estas acciones mediante el resultado de un indicador asociado. Una vez resuelto el problema, es necesario compartir aprendizajes y extenderlos a casos similares mediante formación. Si tras esta etapa no se resuelve el problema, se vuelve a abrir la investigación del GSTD analizando de nuevo causas potenciales o bien, si no hay cabida, se comienza un DMAIC básico.
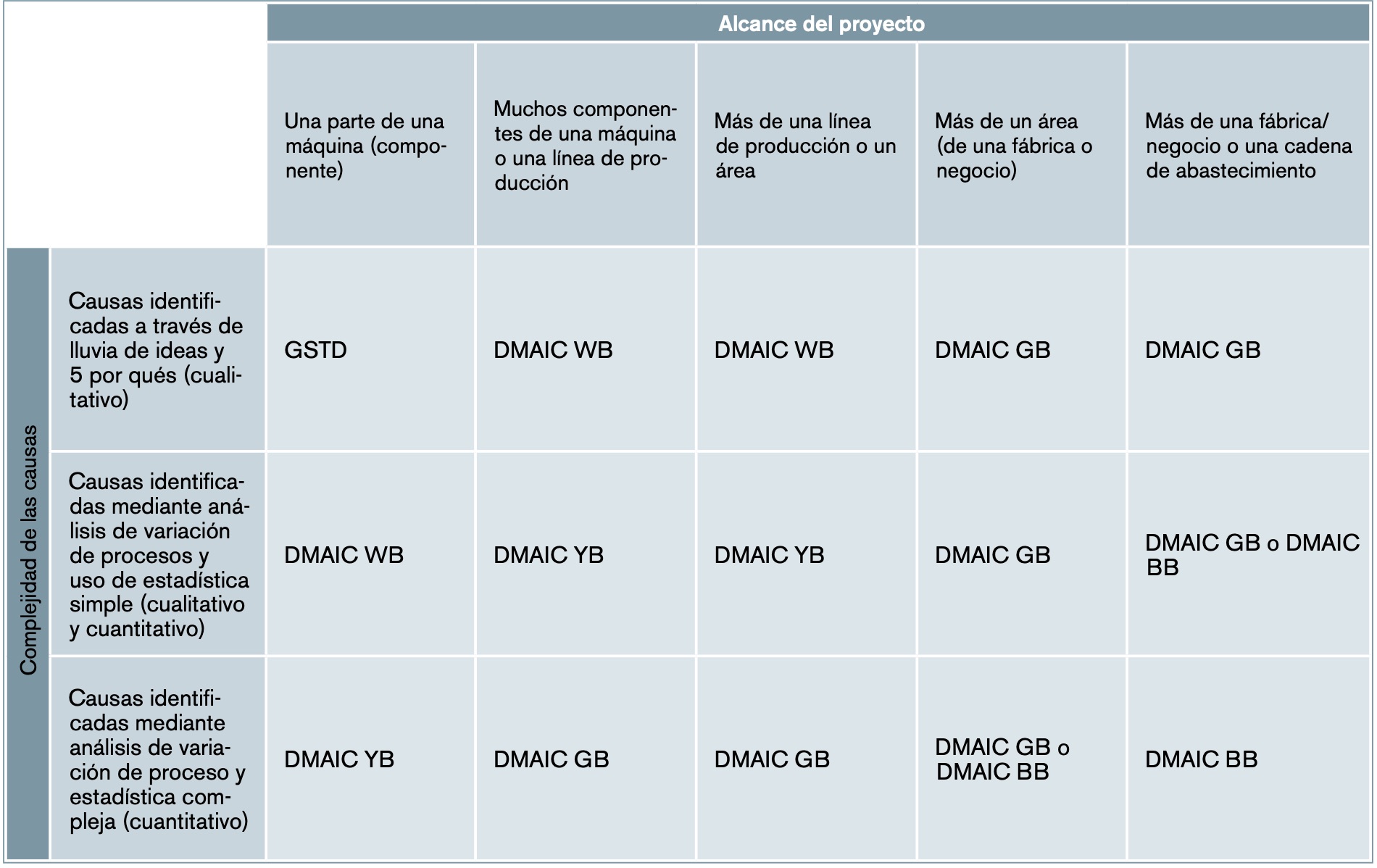
Herramienta DMAIC
DMAIC es una herramienta que sirve para resolver problemas más complejos (Garza et al, 2016), en la que la causa raíz es desconocida ya sea porque:
a) No se han podido resolver mediante un GSTD.
b) Bien por ser problemas recurrentes que no se han intentado resolver y están alineados con las necesidades del negocio.
c) O bien problemas que en su naturaleza requieren desde el origen tener que recopilar datos para su análisis (no se trata de un problema inmediato).
Los proyectos DMAIC, en función de su complejidad, cuentan con diferente rango como sucede en las artes marciales con los colores de los cinturones.
- White belt (cinturón blanco): DMAIC WB.
- Yellow belt (cinturón amarillo): DMAIC YB.
- Green belt (cinturón verde): DMAIC GB.
- Black belt (cinturón negro): DMAIC BB.
En la siguiente tabla se presentan las herramientas usadas tanto en la resolución básica (GSTD) como en los diferentes grados de proyectos DMAIC en función de su complejidad (tabla 2). Por tanto, las personas que lideran estos proyectos deben estar certificadas en las herramientas que se emplean para poder sacar los resultados que se esperan guiando al equipo multidisciplinar de trabajo hacia buen puerto. Su proceso de resolución se estructura en 5 etapas:
1. Definir el problema (D): hay que conocer qué problema se quiere resolver de forma clara y precisa para fijar el alcance del proyecto. Es crucial esta etapa para marcar el camino del proyecto. En esta etapa se identifican los indicadores que se van a utilizar para medir la efectividad del proyecto, se recopilan los datos históricos, se fija el objetivo en función de la mejora que se espera alcanzar, el impacto financiero del proyecto, el equipo multidisciplinar que va a participar (en función de las habilidades que se requieran), se selecciona el indicador o indicadores que servirán para evaluar el éxito del proyecto, los beneficios que se esperan obtener y el plan de trabajo del proyecto en un cronograma. Para poder llevar a cabo esta etapa con éxito es básico que se haga con un consenso claro de lo que se pretende conseguir seleccionando un objetivo SMART (específico, medible, alcanzable, realista y en un tiempo) y valorando desde el principio los recursos que se dispone (tiempo de dedicación a las tareas asociadas, disponibilidad de reunión del equipo y medios técnicos). La salida de esta fase es el diagrama del proyecto. Las principales herramientas a usar son el 5W1H y “es o no es” (para definir el alcance general del proyecto), gráfico de datos/Pareto, hoja financiera y hoja de diagrama de proyecto.
2. Medir (M): entender y describir de forma más precisa el proyecto. Solo es posible mejorar aquello que hemos medido y conocemos, para así poder comparar. Para ello, hay que recopilar datos pero es muy interesante saber qué es lo que queremos medir (es muy recomendable establecer un diagrama de flujo del proceso) para poder establecer un plan de recogida (datos consistentes, fiables, con el detalle necesario que queremos después) para luego poderlos estratificar para su análisis. A veces ya se dispone de datos históricos que se pueden emplear para este paso. Con los datos se elaboran gráficos acumulados para observar tendencias y comportamientos (principalmente si se distribuyen de alguna forma conocida), picos y valores anómalos que se eliminan para que no afecten al análisis. Además, se hace una gráfica para ver cómo evoluciona en el tiempo el
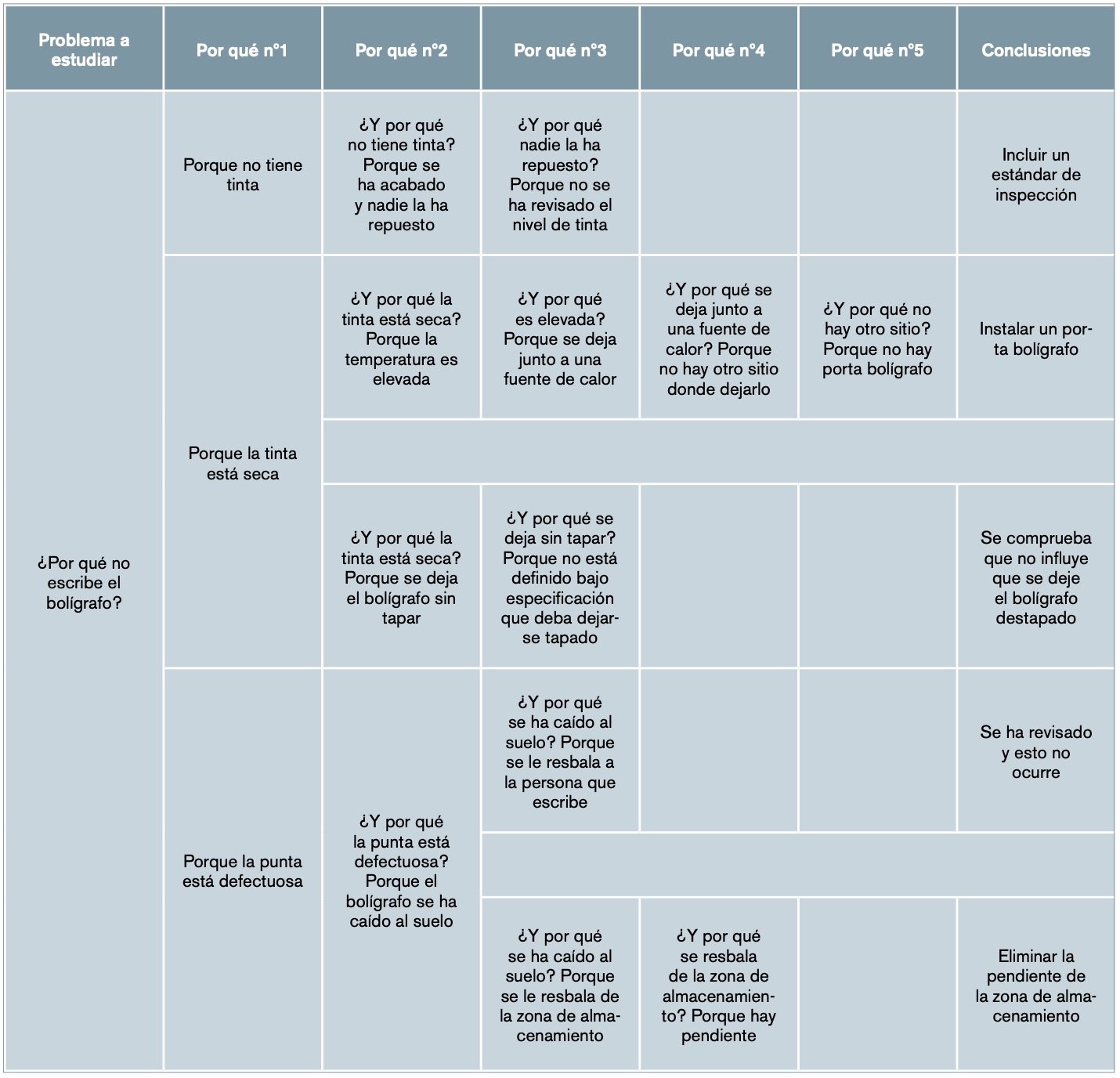
indicador que hemos seleccionado dentro del proyecto para medir su efectividad y así tener la situación de partida). La salida de esta fase es la estratificación de los datos recopilados para su posterior análisis. Las principales herramientas son la hoja de recogida de datos (para que las diferentes personas implicadas en recoger datos lo hagan siempre de la misma manera), estratificación de los datos, diagrama de Pareto, diagrama de flujo y el 5W1H (para definir la declaración del problema y ver su alcance específico ya con más información). Si se detecta que el alcance es muy amplio vale la pena segmentar el problema en problemas más sencillos.
3. Analizar (A): identificar las causas raíz y verificarlas mediante el uso de diferentes herramientas. Si inicialmente ya detectamos que hay partes de la máquina que no están en condiciones básicas, antes de proceder al análisis hay que restaurarlas y si es necesario volver a la etapa de medir. Con toda la información de que disponemos recopilada hasta el momento se procede a realizar una lluvia de ideas con el equipo para identificar las causas potenciales, colocarlas dentro del diagrama de espina de pescado y agruparlas para poder trabajar las causas raíz mediante la realización de un análisis de los 5 por qués. Es muy importante que las diferentes potenciales causas raíz se validen sobre el terreno y se acepten o se descarten.
La salida de esta fase es el conocimiento de las causas que han generado el problema con el mayor grado de detalle, que habrá que verificar. Las principales herramientas son la lluvia de ideas, el diagrama causa-efecto o espina de pescado o diagrama de Ishikawa (Fig. 4), 5 por qués (Tabla 3) y el go & see sobre el terreno para verificar causas supuestamente identificadas.
4. Implementar las mejoras (I): poner en marcha acciones para eliminar causas raíz y verificar su efectividad. A partir de los análisis anteriores ahora ya sabemos las causas que han generado el problema una vez que han sido verificadas. Para ello se propone un plan de acción (con descripción de la acción, plaza y responsable), priorizando el esfuerzo-impacto de cada acción y verificando la efectividad de la solución una vez implantada la mejora. La salida de esta fase es la ejecución del plan de acción para poder verificar la efectividad de las soluciones seleccionadas. Las principales herramientas son la lluvia de ideas, el proceso de priorización mediante el esfuerzo-impacto y el plan de acción.
5. Controlar (C): asegurar el logro de los resultados sostenibles en el largo plazo para garantizar que el problema no vuelve a aparecer, incorporando las soluciones en el día a día mediante la estandarización de los procesos. Este es el momento de establecer los métodos de trabajo para que toda la mejora conseguida perdure en el tiempo, formar al personal en estos cambios y así impedir que vuelva a aparecer el problema. Después de unos 3 meses de funcionamiento de dichos estándares es el momento de volver a medir (como se hizo en la fase 2 del proyecto) y comparar los resultados y cuantificar el impacto financiero real final. La salida de esta fase es la celebración del éxito porque el equipo habrá sido capaz de resolver el problema; será necesario valorar su extensión a otras áreas de la empresa. Las principales herramientas son estándares de trabajo (instrucciones operativas, checklists, lecciones en un punto, etc.), sistemas de entrenamiento y acompañamiento a los operarios en estas sesiones de cambio de forma de trabajo.
Conclusiones
El TPM ha venido para quedarse. A pesar de que muchas empresas en la actualidad no lo tienen implantado, deben ir poco a poco migrando hacia esta nueva forma de trabajo, que no resulta tan nueva en sectores como la automoción, en los que ya llevan muchos años trabajando de esta forma.
Esta metodología establece una documentación, unas reuniones, unos indicadores, unos mecanismos de información muy visuales para saber la situación en la que se encuentra una compañía. Esto es básico para detectar los problemas que van apareciendo, que generan desviaciones con respecto a los resultados esperados. Por tanto, si no queremos que se erosione el resultado final de la compañía y los trabajadores sigan motivados es necesario intervenir.
Parece fácil: los problemas se resuelven siendo disciplinado y utilizando las herramientas adecuadas. En función de la complejidad se requerirá más o menos tiempo o más o menos recursos, pero si hay voluntad de resolución y un buen análisis, finalmente es posible encontrar el plan de acción que elimina el problema de raíz y evita que se vuelva a producir. A veces no es tan sencillo como parece y el problema requiere mucho más tiempo o recursos con respecto a lo que inicialmente estaba previsto, no hay que desmoralizarse.
Una buena foto de la situación real nos ayuda mucho a conducir el problema y a saber los datos que tenemos que recopilar para su resolución. Por ello, es clave que participen las personas que están en el terreno manejando los equipos, que son los que mejor conocen su funcionamiento y las situaciones de no normalidad, tanto del área de producción como del área de mantenimiento.
Por último, es clave implantar las acciones derivadas de las investigaciones y hacer un seguimiento de su utilización. Si no garantizamos esto, todo el esfuerzo realizado no habrá valido para nada porque volverá a su ser inicial.
Bibliografía
Bettina B. (2013). Nestlé Continuous Excellence: Lessons for Driving Performance Improvement. The European financial review.
Climent S (2005). Herramientas de análisis y resolución de problemas utilizadas en los sistemas de gestión de la calidad y su relación con los costes de calidad. Departamento de Análisis Económico, Facultad de Economía Universidad de Valencia.
Garza R., González C., Rodríguez E., Hernández C. (2016). Aplicación de la metodología DMAIC de Seis Sigma con simulación discreta y técnicas multicriterio. Universidad Pablo de Olavide, Sevilla.
GEO Tutoriales (2017). Gestión de Operaciones. Recuperado el 08 de abril de 2019 de: https:// www.gestiondeoperaciones.net/gestion-decalidad/que-es-el-diagrama-de-ishikawa-odiagrama-de-causa-efecto/
Hernández J.C. y Vizán A. (2013). Lean manufacturing: Conceptos, técnicas e implantación. E.O.I. Escuela de Organización Industrial.
Liker J (2004). The Toyota Way. McGraw-Hill Education.
Liker J. y Meier D. (2006). The Toyota Way Fieldbook. McGraw-Hill Education.
Progressa Lean (2018). Expertos en Lean Manufacturing, Kaizen y Mejora Continua. Recuperado el 08 de abril de 2019 de: https:// www.progressalean.com/5-porques-analisis-de-lacausa-raiz-de-los-problemas/
Ruiz J y García E.J. (2015). Aplicación práctica del Lean Manufacturing en el sector de la alimentación. Revista Técnica Industrial nº 310.
Shook, J (2011). How to Go to the Gemba: Go See, Ask Why, Show Respect [Internet]. Consulta el 8 de abril de 2019 de: https://www.lean.org/shook/ DisplayObject.cfm?o=1843
Técnica Industrial, julio 2020, 326: 1-45 | doi:10.23800/10208