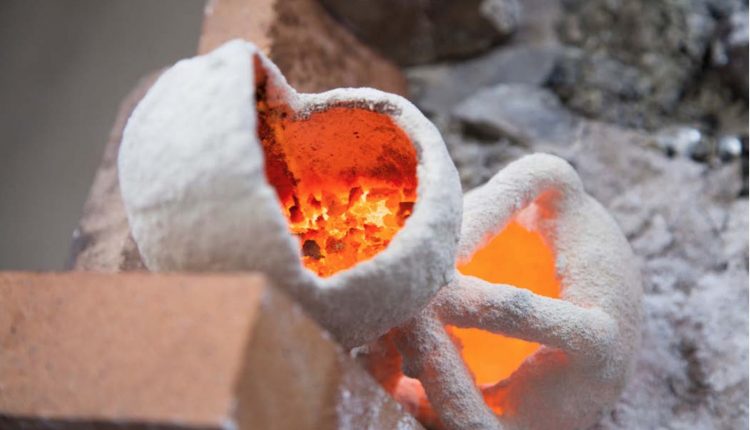
Comportamiento de ceras utilizadas en la microfusión, tras su calentamiento por microondas: técnica de la cascarilla cerámica
Behaviour of waxes used in microfusion, after their microwave heating: ceramic shell technique
Resumen
En este trabajo se abordan metodologías concretas para estudiar el descere de pequeñas piezas de fundición artística mediante calentamiento por microondas. Para ello, se han realizado más de 150 pruebas a fin de comparar el comportamiento tanto de diferentes ceras, como de tamaños y geometrías con figuras de realización propia.
El objetivo es estudiar la empleabilidad del microondas como horno alternativo en piezas de pequeño formato, como pueden ser, piezas de joyería y pequeñas esculturas de metal realizadas mediante la técnica de la cascarilla cerámica. Esta propuesta parte de un proyecto de investigación de la Universidad de La Laguna.
La realización de este trabajo introduce la viabilidad de esta tecnología en campos de la fundición específicos, estudiando su aplicación a unos materiales y técnicas concretas.
Palabras clave: Nuevas tecnologías, descere por microondas, ceras de fundición artística, cascarilla cerámica.
Abstract
This work addresses specific methodologies to study the descent of artistic pieces by microwave heating. In order to get it, more than 150 tests have been carried out to compare the behavior of the different waxes, such as specimen dimensions and geometries.
The objective is based on studying the employability of the microwave as an alternative oven in small-sized pieces such as jewelry pieces or small metal sculptures by using the technique of shell ceramics. This proposal is based on a research project of the University of La Laguna.
The realization of this work introduces the viability of this technology to the fields of specific financing, studying its application to specific materials and techniques.
Keywords: New technologies, microwaves, waxes of artistic casting, ceramic shell.
Recibido / received: 22/12/2019. Aceptado / accepted: 28/04/2020.
1. Francisco Moreno Candel. Doctorando Facultad de Bellas Artes. Universidad de La Laguna.
2. Fátima Felisa Acosta Hernández. Profesora titular del Área de Escultura. Facultad de Bellas Artes. Universidad de La Laguna.
3. Itahisa Pérez Conesa. Profesora del Área de Escultura. Facultad de Bellas Artes. Universidad de La Laguna
Autor para correspondencia: Francisco Moreno Candel. E-mail: pacomorenocandel@gmail.com.
Introducción
Los procesos de fundición artística son antiguos a la vez que sofisticados. En la actualidad, la inclusión de las nuevas tecnologías ha resultado ser un campo de estudio muy recurrido para mejorar los procesos más tradicionales de las Bellas Artes (Díaz, Meier, Pérez y Saorín, 2019). Desde el surgimiento de la fundición hace miles de años, el ser humano ha tratado de encontrar nuevas formas de trabajo hacia su simplificación, adaptación tecnológica, nuevos materiales y calidad del producto (Sorroche et al., 2009).
Actualmente, la producción de piezas en metal fundido sigue siendo delicada y compleja (Albaladejo, 2016), pero gracias a la corriente de información, que caracteriza nuestros días, los métodos de las diferentes disciplinas se retroalimentan con facilidad. A partir de ello, este trabajo tiene como objetivo acarrear dificultades simplificando la infraestructura, abaratando tiempos y costes. Concretamente, se analiza el descere de distintas ceras con la utilización de la energía microondas.
Para la creación de pequeñas piezas de metal fundido, el material utilizado son las ceras. El motivo principal de este uso es que son un material termofusible y reutilizable. Esto permite realizar moldes sencillos a formas complejas, ya que, posteriormente, calentando el molde se extrae el original por derretimiento, dejando así el negativo libre para ser rellenado con metal fundido (Groover, 1997). Para este estudio se han seleccionado las ceras comúnmente utilizadas en talleres de joyería y fundiciones profesionales, para estudiar su calentamiento con microondas, con el fin de posibilitar el descere mediante este sistema, buscando simplificar los procesos de fundición artística, haciéndolos más accesibles y abaratando costes y tiempos de producción.
Diversos materiales se emplean para la realización de los moldes refractarios que varían según las técnicas (Corredor, 1997). En este caso, utilizamos la cascarilla cerámica, no solo por ser el molde referencia de los antecedentes de este trabajo, sino porque su sistema de superposición de capas supone la simplificación las infraestructuras necesarias. Además, su capacidad de registro, porosidad y gran resistencia permite realizar piezas tas como bombas de vacío, centrifugas y hornos eléctricos (Marcos, 2000).
Los sistemas microondas son conocidos y utilizados de manera generalizada en el uso doméstico desde hace décadas. Sin embargo, hoy en día siguen en pleno proceso de estudio debido a que su efectivo funcionamiento requiere del conocimiento de varias áreas técnicas (Plaza, 2015). En la industria, estos sistemas ofrecen ventajas económicas y ecológicas, pero requieren de su continuo estudio para un adecuado funcionamiento, lo cual supone un obstáculo debido a su complejidad, por lo que muchas industrias no apuestan todavía por ello, utilizando equipos tradicionales de calentamiento, ya que su control de temperatura es más fácil de ajustar (Plaza, 2015). Dependiendo de la materia a calentar los microondas actúan con más o menos eficacia (Ramírez, 2010). Esto justifica el interés de este estudio, tratando de estudiar el calentamiento de piezas artísticas determinadas. Se introduce tecnología para mejorar la producción artística, que en muchas ocasiones no puede competir con otras cadenas de producción debido a sus particularidades.
Antecedentes
En el Aula de Fundición Artística de La Universidad de La Laguna se lleva tiempo investigando alternativas metodológicas para los procesos de descere, a fin de mejorar el rendimiento de los talleres de fundición artística. La presente propuesta parte del proyecto de investigación Alternativas al descere en la fundición de cascarilla cerámica (ceramic shell casting): técnica por microondas, trabajo del Departamento de Pintura y Escultura de la Facultad de Bellas Artes. Dicho trabajo desembocó en generar el primer prototipo de horno por microondas para descerar piezas de fundición, cuya patente registrada en España es ES2519990 A1 (07.11.2014). En el estudio de asentar esta técnica novedosa, en la actualidad se está trabajando en la segunda parte de este proyecto, financiado dentro del Plan Nacional de I + D + i. En él se estudia el perfeccionamiento del prototipo horno-microondas, los métodos de descere con el mismo y los susceptores, materiales electromagnéticos absorbentes de microondas utilizados para la eficacia en el calentamiento, con el fin de imitar la técnica del choque térmico empleada en el descere de moldes de cascarilla cerámica. Se han escrito varias tesis sobre fundición (C.Marcos, J. A Aguilar, D. Vila…). La última:Técnica de descere por microondas: identificación, cuantificación y valoración de los susceptores en los estucos de cascarilla cerámica en la fundición artística (Pérez 2017), que estudia el descere por microondas, catalogando y ajustando los denominados susceptores empleados para este proceso. Son materiales aplicados sobre la superficie del modelo en cera a modo de estuco, para facilitar la transferencia de energía electromagnética del microondas hacia una energía térmica, y así, conseguir un calentamiento rápido y eficaz (Pérez 2017).
Actualmente, se desconocen talleres profesionales o docentes que utilicen los sistemas de microondas para descere en fundición. Sin embargo, se sigue trabajando para regular un procedimiento viable para esta alternativa debido a sus ventajas económicas, ecológicas y con menos riesgos.
Objetivos
El objetivo principal es contribuir a la empleabilidad y sistematización de la técnica por microondas en fundiciones artísticas, continuando la línea de investigación mencionada. Se pretende estudiar la adaptación a un sector concreto con materiales y necesidades específicas.
El abanico de ceras utilizadas en el mercado es muy amplio, depende de cada producción. Varía la composición química en función de las propiedades físicas requeridas en cada caso: elasticidad, plasticidad, soldabilidad… Por ello, el primer objetivo ha sido identificar y clasificar las ceras más comunes, para comparar su comportamiento al ser expuestas a la energía MW.
Según la literatura existente, las formas de los objetos a calentar pueden condicionar el calentamiento por microondas generando excesos de campos eléctricos localizados (hot spots) dentro de los hornos. Así pues, la diversidad de formas escultóricas presenta un reto añadido al trabajo. Por ello, el estudio se basa en pruebas concretas a partir de obras escultóricas propias, estudiando formas diversas y variables específicas como pesos, tiempos y materiales, ya que todos ellos pueden generar tensión térmica y variar los resultados.
Material y método
El trabajo parte tanto del estudio de las investigaciones precedentes como del estudio de los campos en los cuales se pretende introducir este tipo de calentamiento, derivando en una experimentación de laboratorio sustentada en una metodología basada en la comparativa de resultados. Se tiene como objeto de estudio las distintas ceras. Sabiendo que la gama de variedades es muy amplia, con la necesidad de acotar, se han recogido los datos necesarios para justificar la elección de cinco ceras muy utilizadas en fundición.
Para el estudio comparativo se ha definido una única variable constante en cada fase de pruebas, como puede ser la cera empleada, la forma de la muestra y el tiempo de exposición, realizando diferentes test de calentamiento.
El horno utilizado ha sido un microondas de uso convencional (OK OMW 2214 B, 800 W) y los sistemas de análisis han constituido la recogida de resultados mediante la medición de temperaturas alcanzadas, pesos de cera extraída y revisión de estado de los moldes cerámicos tras su procesado. Para la realización de muestras idénticas se han diseñado piezas de pequeño formato con formas diferentes atendiendo a curvas, esferas, aristas o picos, ya que los campos eléctricos generados en los MW suponen acumulaciones de energía en determinadas partes (Pérez, 2017).
Las ceras
La cera permite una buena manipulación para la creación de piezas artísticas porque se puede tallar, soldar, colar en moldes y modelar. Dependiendo del tamaño de los modelos, sus formas, detalles y métodos de trabajo unas ceras son más adecuadas que otras. Por ello, hay en el mercado una gran variedad, que reuniendo propiedades comunes, ofrecen particularidades específicas. Hay inyectoras de ceras para moldes que reproducen filigranas muy pequeñas y, para ello, ceras de inyección que alcanzan niveles de licuación óptimos a cierta temperatura, además de producir niveles de ceniza muy bajos tras su quemado, lo que genera figuras de metal pequeñas y precisas: alta joyería (Codina, 2005).
Se utilizan ceras tanto de origen natural como sintéticas buscando una alta capacidad de registro dentro de moldes, elasticidad, puntos de fusión diferentes, dureza, maleabilidad, dilatación térmica, toxicidad y soldabilidad.
Aunque únicamente nos centraremos en las ceras utilizadas para realizar figuras de metal, cabe decir que el espectro de ceras es muy amplio. En palabras de Herrera (2005), director de Iberceras (empresa especializada en diseño y producción de ceras):
«La definición mayoritariamente aceptada es, como el grupo de sustancias o compuestos orgánicos sólidos a temperatura ambiente, fácilmente fusibles, untuosas, con brillo característico, insolubles en agua y solubles en disolventes orgánicos… son termoplásticas, aunque no se les considere polímeros (p. 2).»
Hay muchas aplicaciones en la industria, como adhesivos, en protectores aislantes, barnices, pigmentos y en alimentos. Normalmente no consisten en un solo compuesto químico, sino en mezclas bastante complejas: oligómeros o polímeros en muchos casos, componentes que difieren en su peso molecular, su distribución y/o en el grado de ramificación de la cadena.
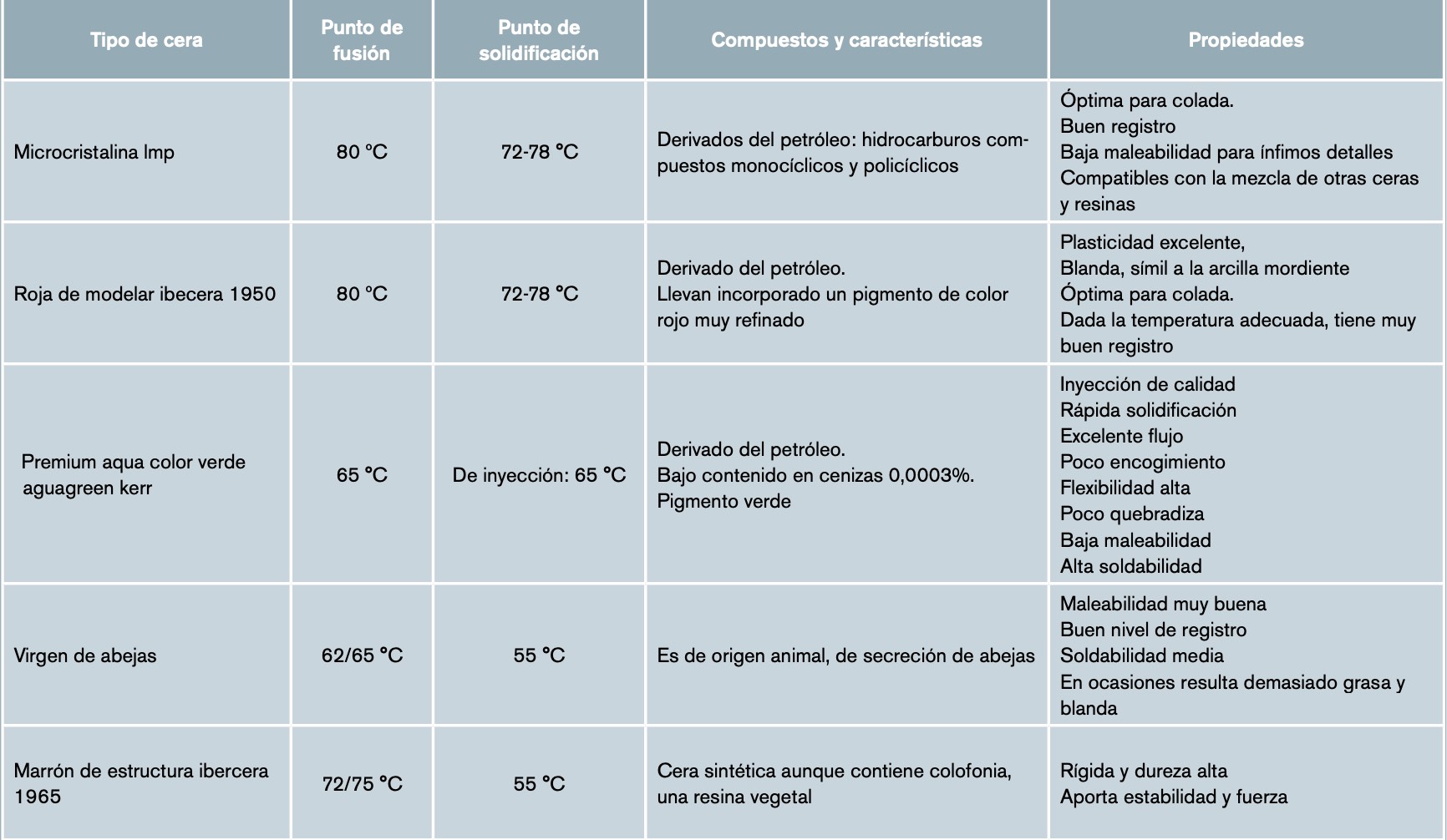
Una definición amplia y útil para fundición la realiza la Asociación Alemana de Ciencias Grasas (Deustche Gesellschaft, 2018), que dice:
«La cera es todo producto natural o sintético que presenta las siguientes propiedades:
• A 20 ºC deben ser de aspecto amorfo a finamente cristalino, de transparente a opaco, de blanda a dura y de plástica a quebradiza.
• Funde a temperaturas superiores a 40 ºC sin descomposición.
• Se pueden pulir bajo una ligera presión.
• Presentan baja viscosidad a temperatura ligeramente por encima de su punto fusión.
• La viscosidad decrece paulatinamente al aumentar la temperatura.
• Su consistencia y solubilidad dependen directamente de la temperatura.
• Generalmente, arden con una llama fuliginosa después de la ignición.
• Pueden formar pastas o geles.
• Presentan baja conductividad térmica y eléctrica.»
Estas características son el motivo de su uso en escultura. Se pueden clasificar según su origen y composición, dividiéndose en tres grupos: naturales, minerales y sintéticas. En otro estudio, Herrera (2008) las distingue en:
«Las primeras exhiben su carácter céreo sin tratamiento químico, mientras que las últimas suelen adquirir su propiedad cérea en el curso de la síntesis. Con respecto a las ceras minerales, aunque son de origen natural, ya que proceden de yacimientos o minas, tienen propiedades muy diferentes (p. 10).»
El prototipo histórico en fundición es la cera de abejas debido a su fácil adquisición unida a buenas prestaciones. Por estas razones ya era muy popular en la antigüedad y aún se utiliza en la actualidad. En el Aula de Fundición de la Universidad de La Laguna (ULL) es el material utilizado, y aunque nos centramos en analizar otras, esta supone un referente comparativo durante toda la fase de pruebas por los conocimientos que se tiene sobre ella, por su uso generalizado y por guardar relaciones físicas con las otras ceras.
Para seleccionarlas, en este estudio, se han clasificado en tres grupos: de inyección (específicas de joyería), de modelar (específicas de escultura) y naturales (por los motivos explicados). Comercialmente, también se diferencian por el formato en el cual se presentan. Por ejemplo, en forma de lentejas las adecuadas para introducir en las inyectoras o en láminas finas para realizar trabajos con planos, como podría ser unos pétalos de rosa. Sin embargo, guardan semejanzas a nivel químico y, por tanto, también en su comportamiento físico, objeto de interés en el estudio de su tratamiento térmico. Resulta propio mencionar que sus colores también pueden asociarse con clasificaciones comerciales, pero no siempre son afines entre ellos en cuanto a sus propiedades. Normalmente, se trata de una simple adhesión de pigmento. También, en ocasiones, el valor cromático busca facilitar el visionado del volumen para el trabajo escultórico. Las ceras de inyección deben ser fluidas, de baja densidad y muy elásticas, pero resultan poco maleables a diferencia de las de modelar, que aunque son más densas, se pueden utilizar también para colado en moldes y presentan, sin embargo, menos elasticidad. Por eso, son más frágiles a los golpes (Codina, 2005).
Tras visitas en diferentes talleres, pruebas propias y consulta en la literatura existente, se seleccionan para este estudio los siguientes elementos: la cera roja de modelar, cera de abeja (muy comunes en talleres de fundición profesionales), la aquagreen de inyectora (muy utilizada en talleres de joyería), la cera microcristalina blanca y la cera marrón de estructura (utilizadas complementariamente en mezclas directas o indirectas). En la tabla 1 se recogen los datos concretos de las ceras analizadas.
Tecnología microondas
Antes de empezar a contrastar el comportamiento de las ceras, es importante conocer el funcionamiento del microondas, ya que su buen funcionamiento viene directamente relacionado con la materia a calentar, es decir, el factor de pérdidas energéticas que esté presente será condicionante.
Las microondas son ondas electromagnéticas comprendidas en la banda de frecuencias entre los 300 MHz y los 300 GHz. Las bandas utilizadas para las aplicaciones de procesado de materiales con microondas son las conocidas como ISM, bandas de uso libre con algunas restricciones, destinadas para aplicaciones industriales, científicas y médicas. Las más empleadas son las frecuencias 915 MHz, 2.450 MHz y 5,8 GHz (Plaza, 2015). Entre estas ventajas, y para no extendernos, destacaremos considerar que el calor en estos hornos se genera directa y únicamente con el objeto de calentar, a diferencia de los hornos eléctricos o de gas convencionales, en los que el calor se emite por conducción, desde el exterior de la pieza hasta el interior del material con la necesidad de acondicionar térmicamente toda la cavidad del horno y, por tanto, derrochando más energía (Mujumdar, 1995; Meredith, 1998). Es decir, es necesario mantener la cavidad del horno a una alta temperatura, aumentando con ello el empleo de riego energético. Por esta razón, la eficiencia energética de los microondas, a priori, vence, pues la energía microondas ataca directamente sobre el material evitando pérdidas de calor. Sin embargo, el uso eficaz de estos sistemas requiere de un conocimiento específico y especializado, ya que el problema viene cuando las propiedades dieléctricas del material a calentar no son las adecuadas y, por tanto, requieren de mucho tiempo de exposición frente a las microondas.
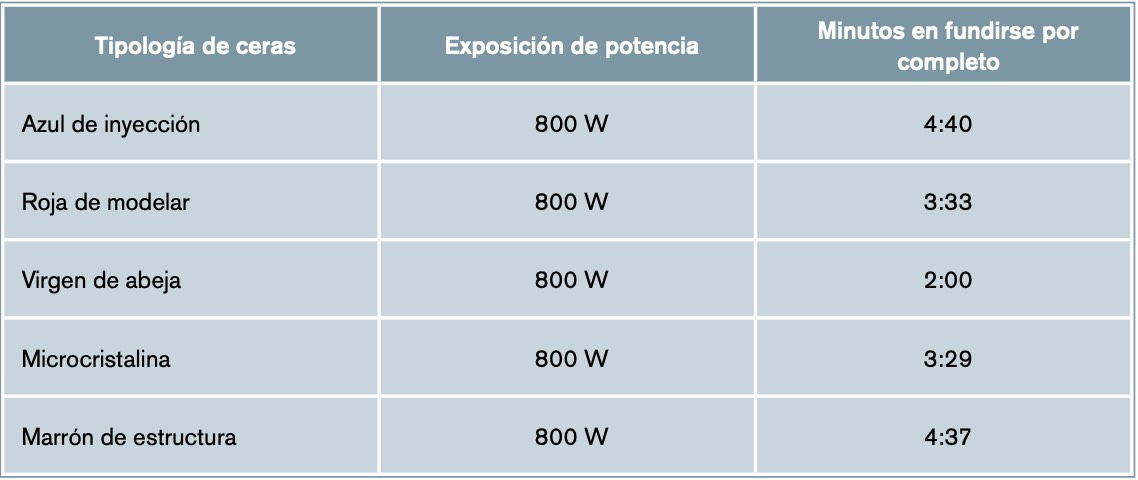
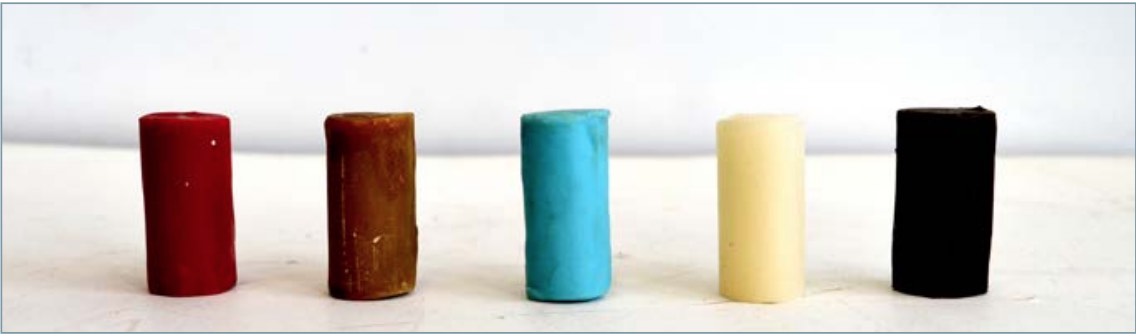
El aparato microondas empleado para este trabajo es el OK OMW 2214 B. Se trata de un aparato comercial económico y pequeño que se utiliza para el calentamiento de alimentos en uso doméstico. Dispone de un programa de cinco niveles de potencia con temporizador y la homogenización del calentamiento mediante plato giratorio.
Resultados y discusión
Pruebas de reconocimiento e identificación de ceras bajo exposición de energía de microondas
En primera instancia surge la necesidad de conocer el comportamiento de las distintas ceras al ser expuestas a la energía microondas: su capacidad de absorción de microondas es determinante para controlar su comportamiento en el interior de los moldes. Para ello, se han realizado cinco muestras de igual formato (figura 1) para introducirse en el horno MW, averiguando así, el tiempo en que se funden por completo, como se observa en la tabla 2. De esta manera, se averigua de forma práctica qué capacidad tienen de absorción cada una de las ceras. La probeta utilizada en las pruebas iniciales consiste en un cilindro de 0,5 cm de diámetro y 2 cm de altura.
Así bien, para concretar su funcionamiento a un tiempo determinado, se han realizado pruebas en las que el factor tiempo es invariable. Estimando lo ideal, se ha considerado que para estos modelos, 2 minutos de tiempo es suficiente, teniendo en cuenta el peso de cera introducida. Buscando conocer sus capacidades dieléctricas de una forma experimental, se plantea el estudio consistente en calcular el peso de cera derretida tras la exposición de muestras idénticas a tiempo constante. Por ello, el peso es la referencia y cuanto mayor sea el peso de cera derretido, mayor capacidad de calentamiento tendrá la cera.
Con la finalidad de extraer los resultados más certeros posibles, se realizan 10 muestras con cada cera. De este modo los datos medios obtenidos son una guía fiable. Los gramos que se indican en la tabla 3 presentan la cantidad media de cera que se ha evacuado.
Con estas pruebas iniciales se ha determinado que, teniendo en cuenta que una pieza de un formato muy pequeño expuesta al 100% del rendimiento (800 W) da como resultado tiempos largos en comparación a 2 minutos, se establece que los resultados de cera evacuada son poco efectivos.
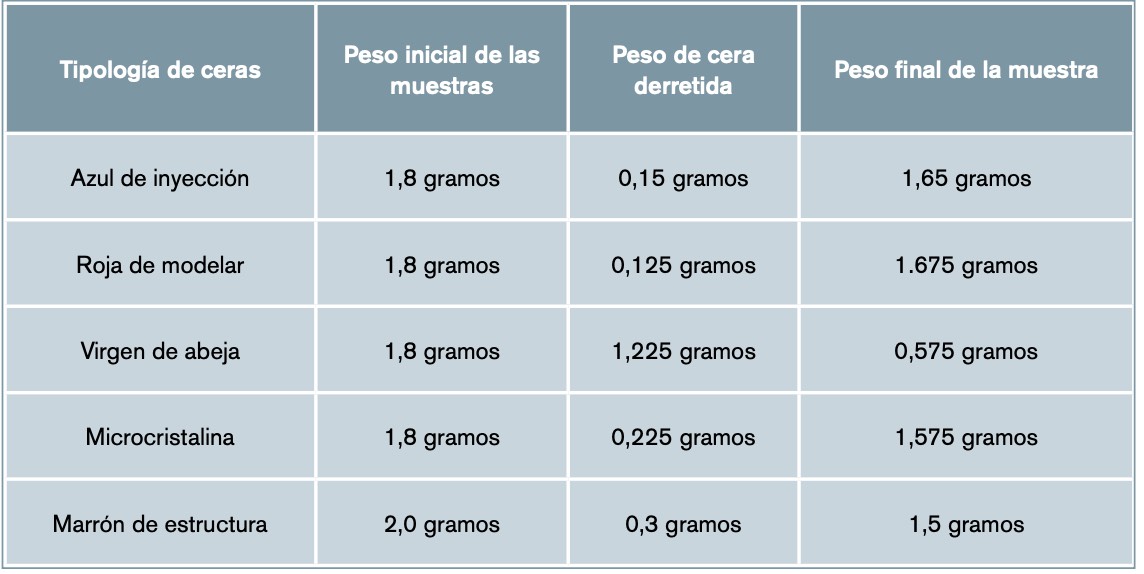
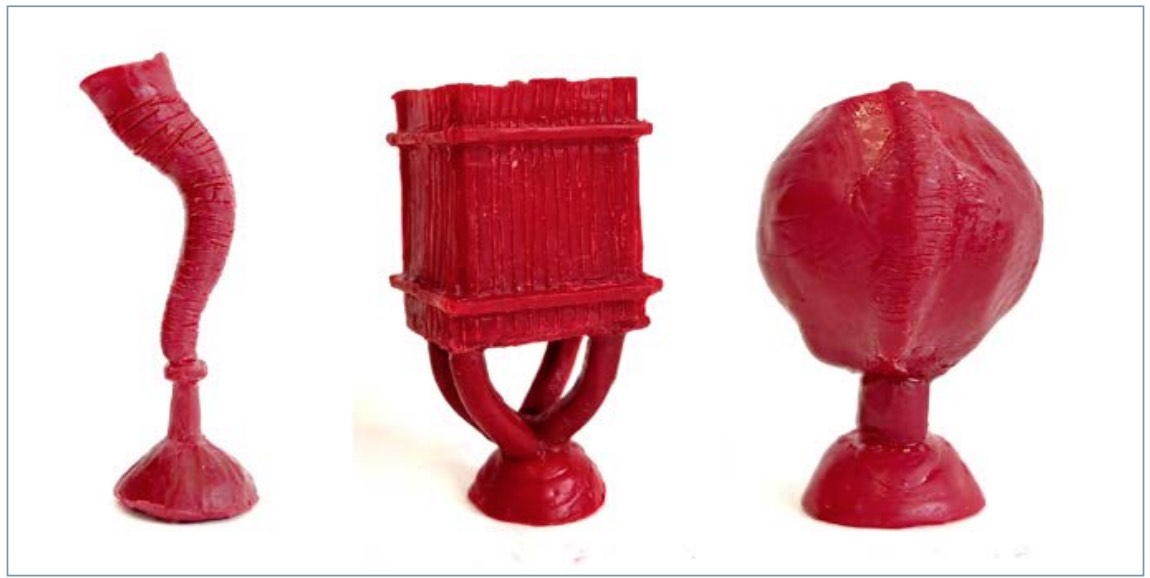
A partir de ello, se barajan dos premisas que establecen el objeto de estudio, sabiendo los resultados obtenidos en investigaciones que preceden al trabajo: un cilindro de apenas 1,8 gramos no es resultado óptimo que en 2 minutos se descere tan solo el 8% aproximadamente del peso del total. Por tanto, se plantea que si un volumen tan pequeño y compacto en esta cavidad tarda tanto tiempo en derretirse puede ser por dos razones: o bien las microondas necesitan ser más potentes para que atraviesen la masa, o bien el formato de esta probeta, tipo dado cilíndrico, es poco efectivo por la baja exposición volumétrica que ofrece para captar la irradiación de ondas dentro de la cavidad del horno. Así pues, teniendo en cuenta que este trabajo está dirigido a piezas de pequeño formato, normalmente con ramificaciones, volúmenes dispares y secciones delgadas, podrá variar el calentamiento según la forma. Este fenómeno plantea el núcleo inicial del trabajo: la geometría de las formas difiere en la eficiencia del calentamiento microondas.
Estudio de las ceras en función de la morfología de las piezas
Tras las pruebas iniciales de identificación, se realizan pruebas de verificación con modelos de formas diversas para identificar y sistematizar las variables según las mismas. Se ha comprobado que el calentamiento de las diferentes ceras empleadas en este estudio es seguro y que, además, es similar entre ellas, a excepción de la cera virgen de abeja, la cual se calienta más rápido. Esto se debe a que al ser una cera 100% natural contiene más humedad molecular.
La finalidad es estudiar las diferentes ceras empleadas en joyería y escultura para poder ser desceradas con la energía microondas, pero se añade la necesidad de estudio de formas, por lo que queda instaurada en la investigación. En referencia a la bibliografía existente, se sabe que el eficaz calentamiento por microondas está relacionado no solo con la materia y su masa, sino también con su forma. Esto se debe a los campos eléctricos generados dentro del horno por la manera de penetrar las ondas en los materiales. Según Pérez (2017):
«Durante la fase del proceso experimental y la lectura de los resultados, se demuestra que el formato de la pieza, su volumen y su forma, incluso la disposición del árbol de colada, repercute en el tiempo de descere. Comparando la muestra S.A+G (formato ‘sándwich’) con la probeta C.A+G (formato ‘minicúpula’) se aprecia que la diferencia de tiempos de descere es notable, siendo las primeras en tiempos más largos, en torno a los 60 s de media y en las segundas unos 40 s de media, incluso sabiendo que las segundas contienen más cantidad de cera que las primeras (p. 174).»
Esto significa que la forma de la materia influye en su velocidad de calentamiento. Si la forma contiene aristas o partes puntiagudas, como pueden ser texturas o pequeñas filigranas, en estas zonas se localizan “hot spots”, puntos calientes, zonas donde la concentración de microondas es mayor, generando campos eléctricos, y aumentando notablemente la temperatura en ciertos puntos, dejando partes frías en el resto del volumen. Por esto, las formas compuestas por planos, curvas o esferas resultan tener un calentamiento más homogéneo.
Unido a esto, se determina que el volumen que ocupa dentro de la cavidad la materia a calentar repercute en la irradiación: a más volumen, más recepción de irradiación microondas y, por tanto, más calentamiento.
Por ello, se realiza un estudio de formas diferentes para contrarrestar los resultados. Se han diseñado tres probetas de formas que, eventualmente, son recursos morfológicos utilizados en la producción de piezas de joyería o escultura. Terminaciones cilíndricas/esféricas y conformadas por aristas/planos, como se aprecia en la figura 2. La producción de pruebas ha sido seriada mediante la realización de moldes probeta con silicona, y se han obtenido modelos idénticos, de modo que se mantienen las mismas constantes de tamaño, textura, forma, peso y sección, ya que son variables que repercutirían en el calentamiento. Las piezas se presentan huecas y con secciones regulares.
La técnica para el descere por microondas empleada ha sido cascarilla cerámica, cuya mezcla para el molde está compuesta de moloquita y sílice coloidal, realizada mediante la inmersión de los originales en la mezcla, para conseguir un espesor similar en todas las muestras, ya que el grosor influye en la susceptibilidad y resistencia. En estas pruebas se mide la resistencia a la expansión de la cera al calentarse, ya que puede quebrar el molde y generar fisuras. Además de estudiar el calentamiento de las formas, mediante el peso de cera extraída, también se observa la efectividad en el choque térmico mediante la observación del índice de fisuras obtenido en los moldes.
En la técnica de cascarilla cerámica, el molde se genera por superposición de capas, y el número y densidad de la mezcla determina su grosor. En esta ocasión el molde está conformado por tres baños de 50-50%, 40-60% y 30- 70%, con moloquita en harina (-200) y sílice coloidad Hispasil (molécula 7 nm), respectivamente. En cada una de las capas, se proyecta moloquita en granulometría 50/80 en las dos primeras capas, y moloquita 16/30 en la tercera.
Siguiendo la metodología empleada, se realizan series de 10 muestras por cada una de las ceras (figura 3). Manteniendo el factor tiempo (3 min) y potencia constante (800 W), se observa durante el calentamiento gradual la presión que ejerce cada una de las ceras en el molde. La localización de las fisuras y su número determinan la efectividad que tiene el choque térmico en el molde y las tensiones térmicas que se producen según las formas. Se ilustran algunas de las muestras con el revestimiento cerámico en la figura 4.
Procesadas las muestras que tienen como nomenclatura TR, el índice medio de cera recolectada es el 36,46% aproximadamente, unos 1,714 gramos por muestra para todas las ceras. Cabe destacar que la cera virgen de abejas y la cera blanca microcristalina obtienen los mejores resultados, ya que se extraen más gramos, lo cual indica que su calentamiento es más rápido. El índice de moldes con resultados quebrados es del 100%, factor que indica que el calentamiento de la cera es demasiado lento y gradual. Se calienta progresivamente y se expande hasta quebrar el molde cerámico, por lo que se descubre que la eficacia del choque térmico es nefasta. Las fisuras se suelen producir en las zonas más altas o por la mitad, la mayoría de las veces longitudinalmente. En la siguiente tabla se recogen los datos de los promedios obtenidos con cada cera en las probetas forma TR.P (tabla 4).
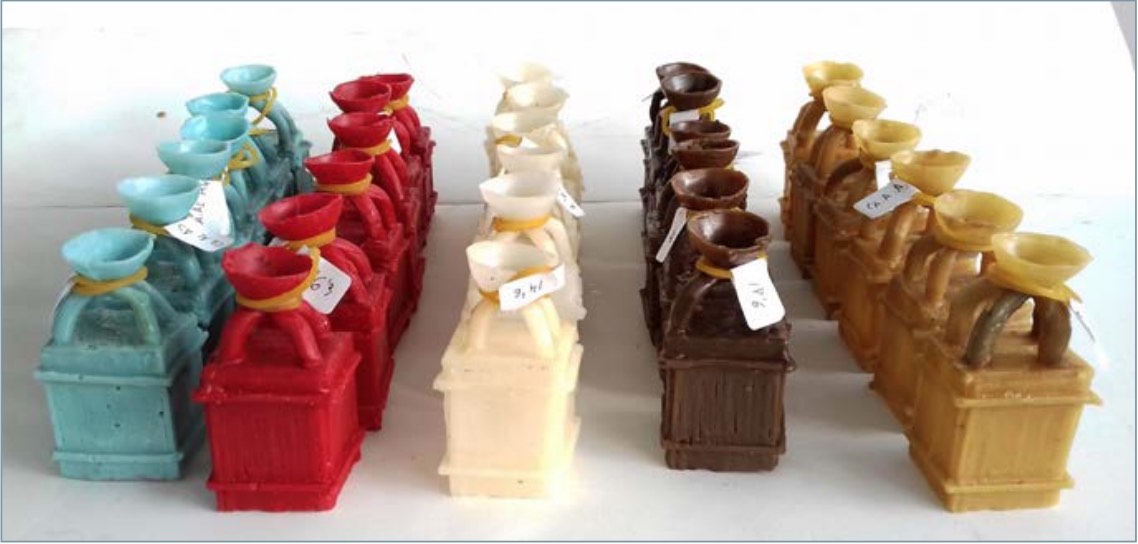
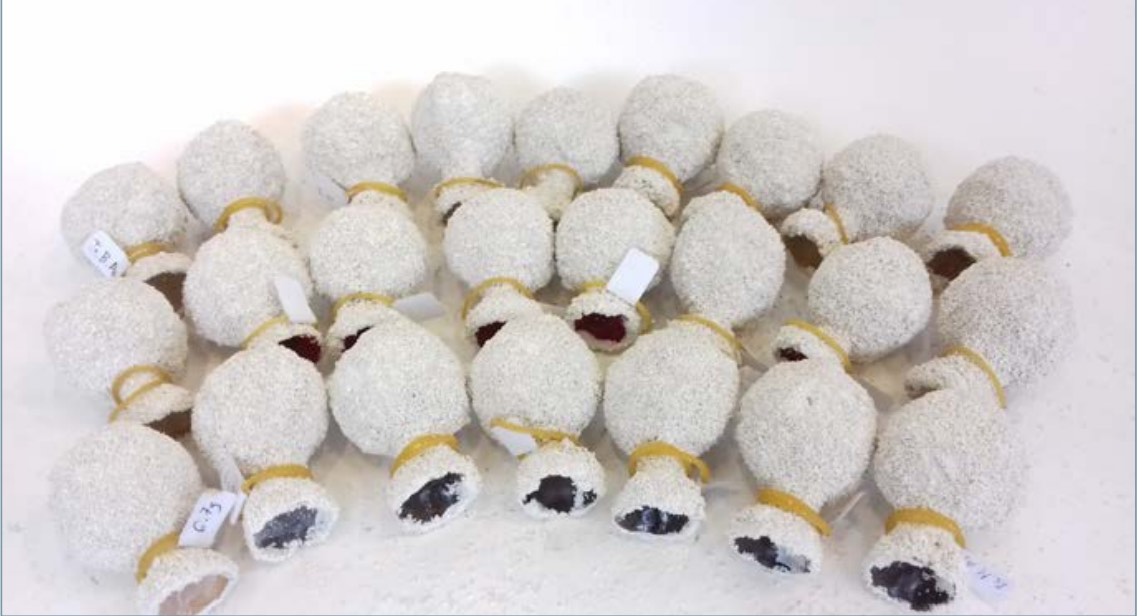
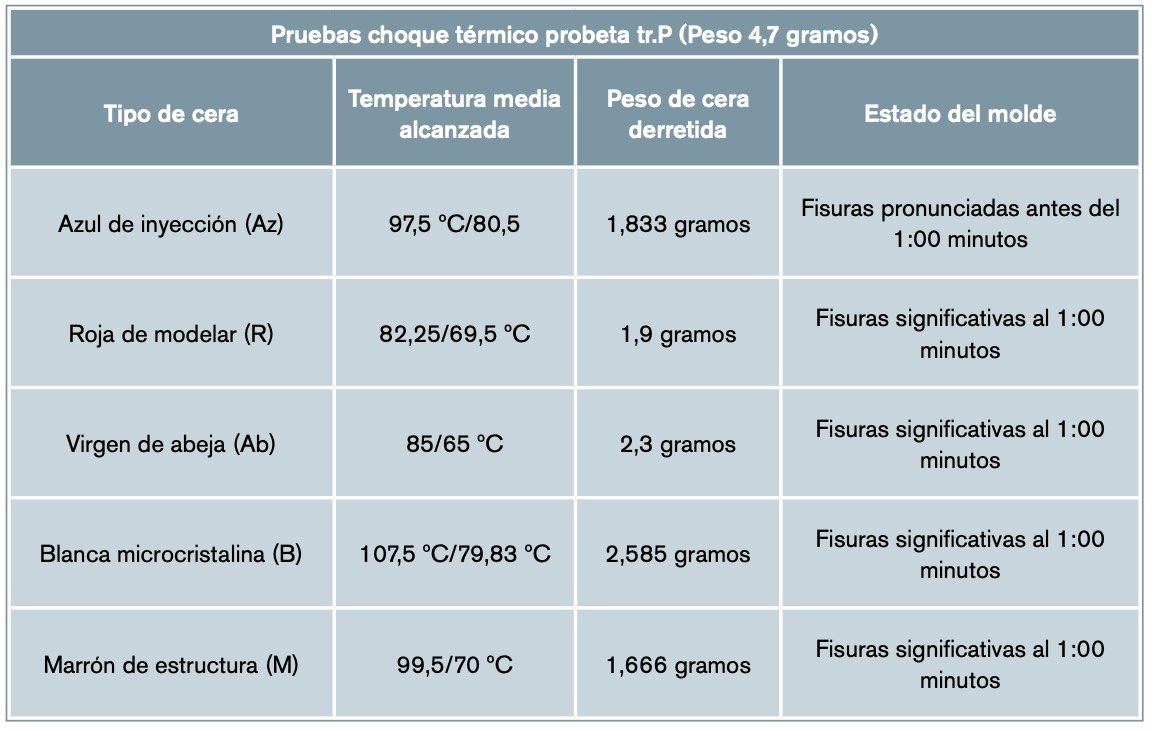
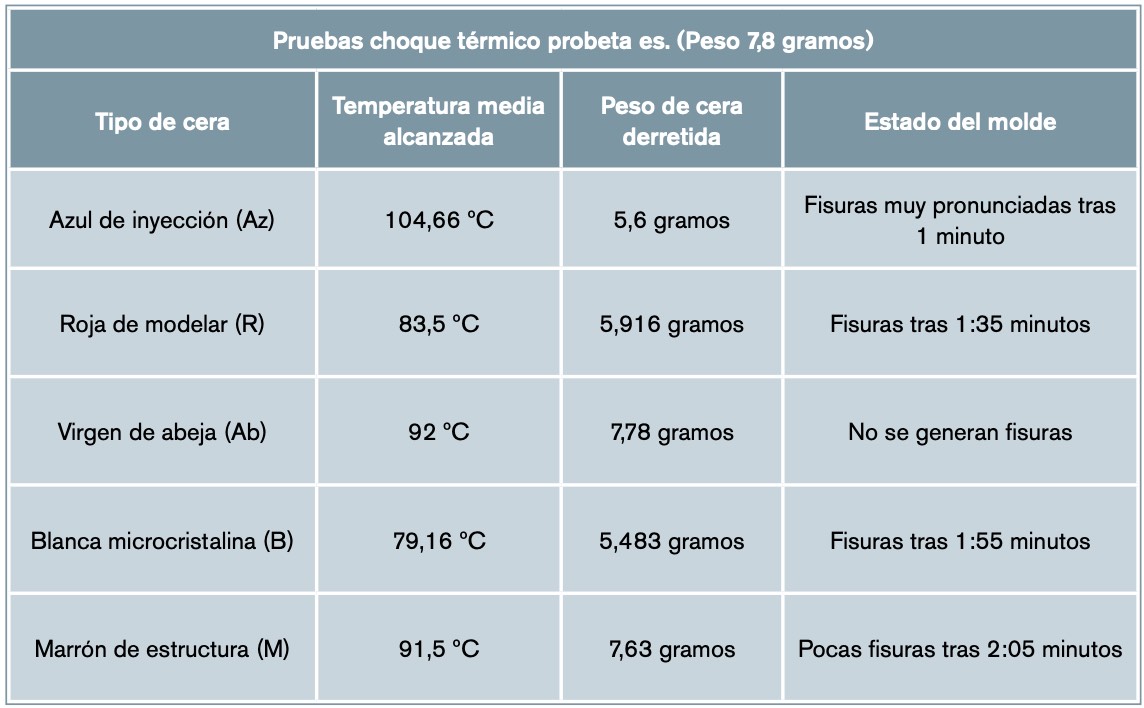
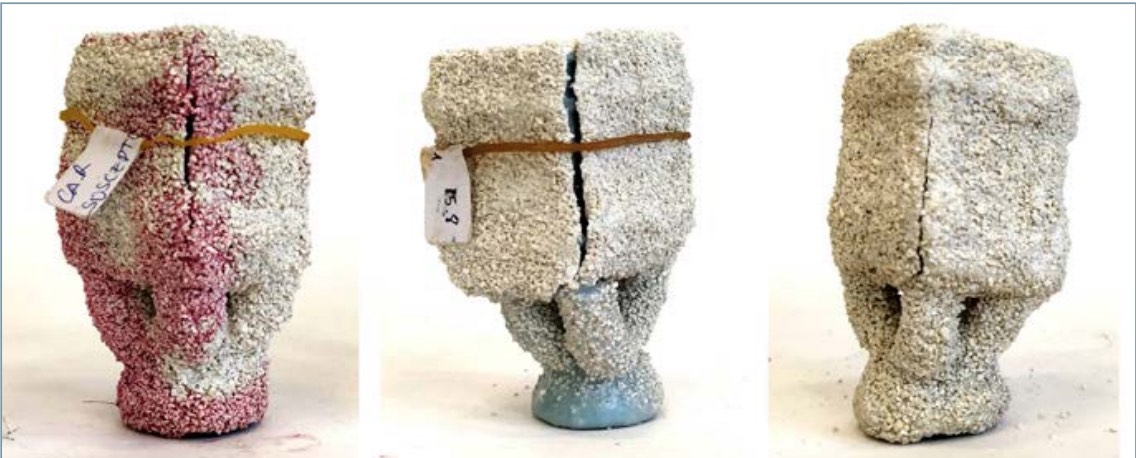
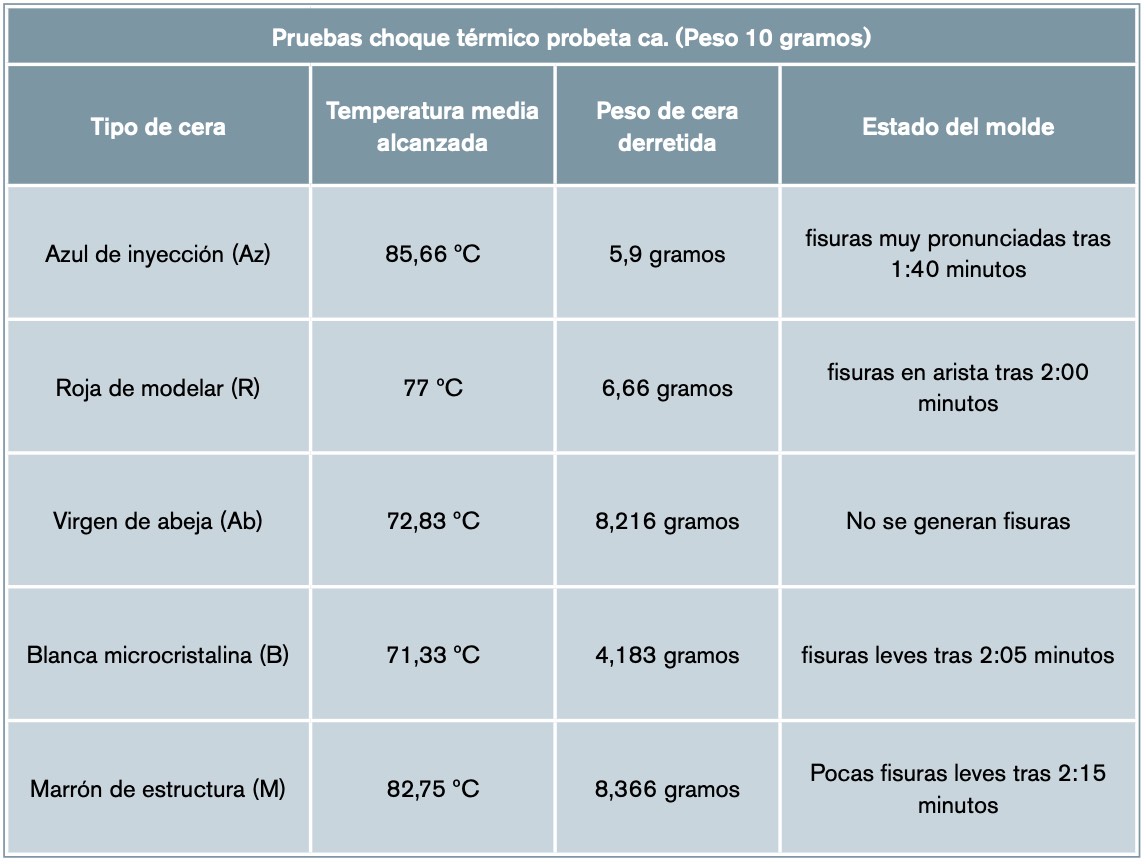
Sin embargo, con las probetas ES. el índice de fisuras es del 83,3%, viéndose reducidas en el 16,7% con respecto a la probeta TR; (tabla 5). Se demuestra, por tanto, que el calentamiento más homogéneo de las formas esféricas produce un derretimiento más estable de la cera, reduce la dilatación térmica de la misma y produce, en consecuencia, menos grietas en los moldes. Las fisuras suelen producirse en las aristas circulares en conexión con el interior del molde o en la mitad del volumen.
El índice de cera recolectada es del 41,23% aprox. con unos 5,4 g por muestra para todas las tipologías de ceras probadas. Sin embargo, la cera virgen de abejas y la cera marrón obtienen los mejores resultados en cuanto a su extracción. La cera de inyección azul turquesa presenta fisuras muy pronunciadas en el molde, pero la cera virgen de abeja no presenta prácticamente fisuras. Esto puede deberse a que la dilatación térmica de la cera azul sea más alta que las demás, unido a unas propiedades dieléctricas más bajas. Resulta lógico que la cera de abeja, al tener un mejor calentamiento, unido a la forma sin hot spots, como es la ES. no tenga grietas en las 10 muestras procesadas. En la siguiente tabla se recogen los datos medios de las pruebas.
En las siguientes pruebas, ilustradas en la figura 5, el índice de fisuras es del 85%. Estas formas cuadradas compuestas por planos ayudan a un calentamiento adecuado debido a la buena recepción de las ondas. Sin embargo, al igual que en la probeta TR. aparecen hot spots que se focalizan en las aristas.
El índice de cera recolectada es del 32,63% con 5,22 g por muestra para todas las ceras. Como se aprecia en la tabla 6, la cera virgen de abejas y la cera marrón de estructura vuelven a obtener mejores resultados en cuanto a su derretimiento. De nuevo, se comprueba que la cera de inyección azul presenta un índice de expansión muy alto con fisuras muy pronunciadas en el molde. Los moldes con la cera virgen de abeja no presentan tensiones.
Conclusiones
En este trabajo, al no hacer uso de susceptores microondas adicionales que aumenten la temperatura en el material para la imitación del choque térmico, se ha podido observar los comportamientos de las ceras en el recubrimiento cerámico y estudiar los resultados de fisuras aparecidas en los moldes según ceras y formas.
Concluido el estudio, se ha comprobado que las ceras sintéticas utilizadas en fundición tienen un calentamiento más lento que las ceras naturales, concretamente la cera de abeja 100% natural, probablemente, debido a que contiene más humedad molecular y es un material más absorbente a las microondas. También se ha comprobado que la cera marrón y la cera blanca microcristalina tienen un calentamiento más rápido que la cera roja de modelar y la azul de inyección, puesto que la cantidad de gramos de cera derretida de estas primeras ha sido mayor en todas las pruebas. Esto puede deberse a que la cera marrón contiene una resina natural en su mezcla y, por tanto, más humedad que el resto de las sintéticas. Además, se observa que la cera blanca microcristalina, con una densidad mucho menor a las demás, tiene menos fuerza para quebrar los moldes y se filtra al expandirse en los poros del molde sin romperlo.
Por otro lado, se ha comprobado que las tensiones térmicas que han provocado fisuras en las muestras (TR.P) son bastante violentas, y son más pronunciadas las construidas con la cera azul de inyección. Esto se debe a que la forma genera más hot spots, unido a que la cera azul es la que más lentamente se calienta y mayor dilatación térmica tiene. Sin embargo, las formas esféricas construidas con la cera marrón y la de abejas, no presentan prácticamente fisuras. Esto determina que la expansión térmica en estos formatos no es peligrosa para el molde y que se podrían realizar variantes de potencias para ajustar un descere óptimo sin tener que hacer uso de aditivos de temperatura.
En las probetas de planos y aristas (CA) y (TR.P), se observa que las tensiones en las aristas suele quebrar el molde. Ambas son formas delicadas porque los planos y las aristas generan posibles hot spots dentro del microondas. Sin embargo, se han obteniendo resultados mejores, con menor índice de fisuras, en las probetas (CA) que en las (TR.P). Esto demuestra que cuando una escultura abarca más superficie expuesta a las ondas, esta acumula más energía porque capta más irradiación. Por tanto, no solo las propiedades dieléctricas de los materiales influyen en la velocidad de calentamiento, sino que el grosor y la forma de los objetos, además de su posición en la cavidad del horno, interfieren notablemente en la velocidad del calentamiento. Además, en las probetas dado cilíndrico (1,8 g) (v. figura 1), la materia empieza a derretirse a los 2 minutos, mientras que en las probetas (TR.P) (v. figura 2) en tan solo 1 minuto la cera ya se ha derretido y expandido, pese a tener un peso superior, más masa que la otra: 4,7 gramos. Por eso, se puede afirmar que la forma influye en la velocidad de calentamiento: a mayor volumen, con menor masa, mayor velocidad de calentamiento; a menor volumen, con masa comprimida, menor velocidad de calentamiento. Esto es por la exposición del volumen a la irradiación de ondas dentro de la cavidad.
Paralelo a ello, se ha comprobado que las formas puntiagudas y con aristas generan puntos muy calientes hot spots, concentrando irradiación microondas en estas partes a causa de los campos eléctricos. Consecuencia de ello, quedan partes más frías en el resto de la muestra. Esto se ha visto en las probetas (TR.P). Sin embargo, en la forma esférica (ES), no se producen hot spots y el calentamiento se reparte homogéneamente. En este caso, se extrae más cera en menos tiempo, produciendo menos fisuras en el molde refractario, mientras en otras formas, se complica el método, pues una de las premisas principales para reproducir el sistema de choque térmico en el descere de la cascarilla cerámica es obtener un calentamiento rápido que logre evacuar el molde de cera antes de que la expansión de esta lo quiebre.
Por todo ello, se presume que las diferentes ceras que se utilizan para joyería y escultura son productos que presentan características buenas para introducir la tecnología microondas en los talleres, ya que son susceptibles a las microondas y nada peligrosas. Sin embargo, la imitación del choque térmico requiere en algunas ceras (azul de inyección) y formas (puntiagudas y aristas) susceptores que aceleren el calentamiento. Sin embargo, otras ceras (naturales) y formas (esféricas y curvas) son válidas sin ellos. Con este trabajo se plantean nuevas vías de investigación con microondas para realización de piezas en moldes que no requieran choque térmico, como los yesos refractarios, con un alto contenido de humedad y, por tanto, susceptibles a las microondas, pues esta tecnología abarata costes de infraestructura y tiempos de procesado y reduce la emisión de tóxicos en confrontación con las combustiones de otros métodos que producen llama. En definitiva, suponen una mejora en los procesos de fundición artística haciéndolos más accesibles para pequeños productores, artistas y artesanos.
Referencias
Albaladejo, J. C. y Rodríguez González, I. (2006): Fundición a la cera perdida: Cellini y la magnetita. Universidad de La Laguna- Bellas Artes 14.
Codina, C. (2005): La técnica y el arte de la joyería explicados con rigor y claridad. Parramón Ediciones, Barcelona, 116-118.
Corredor Martínez, J. A. (1997): Técnicas de fundición artística. Universidad de Granada, 214.
Díaz Alemán, D.; Meier, C; Pérez Conesa, I.; Saorín, J. L. (2019): Fundición artística de objetos complejos impresos en 3D con PLA (ácido poliláctico) como alternativa al modelo de cera. Arte, Individuo y Sociedad, Madrid, 545.
Groover, M. (1997). Fundamentos de manufactura moderna. México, 1997, p. 243.
Herrera Muñoz, D. (2005). Las ceras introducción y aplicaciones. Iberceras (SA). Revista IDE, Madrid, 2.
Herrera Muñoz, D. (2008). Historia de las ceras y sus aplicaciones. Iberceras (SA). Revista IDE, Madrid, 2.
Marcos Martínez, C. (2000). Fundición a la cera perdida: Técnica de la cascarilla cerámica. Universidad Politécnica de Valencia, 46.
Metaxas, A. C. & Meredith, R. J. (1983). Industrial Microwave Heating. Peter Peregrinus Ltd., Londres.
Monzó Cabrera, J. (2002). Estudio Del Secado Asistido Por Microondas En Los Materiales Laminares. Tesis doctoral, Murcia.
Pérez Conesa, I. (2017). Técnica de descere por microondas: identificación, cuantificación y valoración de los susceptores en el estuco de cascarilla cerámica para fundición artística. Universidad de La Laguna, p. 58-176.
Plaza González, P. J. (2015). Control de la temperatura en sistemas de calentamiento por microondas. UPV, p. 8-9.
Ramírez Gil, F. J. (2010). Comparación entre las técnicas convencionales y las microondas para la conformación y secado de materiales cerámicos fabricados por colado. Colombia 16.
Sorroche Cruz, A.; Lozano Rodríguez, I. l.; Durán Suárez, A. J.; Peralbo Cano, R.; Bellido Márquez, C. (2009). Mejora de los métodos de trabajo en la fundición escultórica con modelos de poliestireno expandido. Revista Técnica Industrial, 2009, p. 1.
Vila Moscardó, D. (2015). La revolución de la cascarilla cerámica. Universidad Miguel Hernández, Alicante, p. 211.