Herramienta de bruñido con puntas intercambiables para el acabado de moldes
Burnishing tool with interchangeable tips for mould finishing
Jordi-Adalbert Marqués Salvador (1), Ramón Jerez-Mesa (1), Jordi Llumà (2), J. Antonio Travieso-Rodriguez (1)
Resumen
En esta contribución se presenta el resultado del diseño, la fabricación y puesta a punto de una herramienta de bruñido para ser utilizada sobre distintas superficies previamente mecanizadas mediante fresado. El objetivo es diseñar y fabricar una herramienta capaz de conseguir superacabados de algunas superficies de moldes y matrices. Más concretamente la herramienta ha sido diseñada con el fin de disminuir la rugosidad de la superficie de partes de moldes para inyección de plástico y aluminio, los cuales actualmente, se pulen a mano. La herramienta se puede montar en cualquier centro de mecanizado de 3, 4 o 5 ejes y permite bruñir gran parte de la superficie. Se han realizado pruebas sobre un molde de acero X40CrMo5V5-1 para comprobar su efectividad. Los resultados obtenidos han sido satisfactorios, por lo que se ha cumplido con las expectativas planteadas por el cliente.
Palabras clave: Bruñido, rugosidad superficial, fresado.
Abstract
This contribution presents the result of the design, manufacture and fine-tuning of a burnishing tool to be used on different surfaces previously machined by milling. The goal is to design and to manufacture a tool capable of superfinishing some moulds and array surfaces. More specifically, the tool has been designed in order to reduce the roughness of the surface of parts of plastic and aluminum injection casts, which are currently polished manually. The tool can be mounted on any 3-, 4- or 5-axis machining center and it allows to burnish large areas of the surface. Tests have been carried out on a X40CrMo5V5-1 steel mould to verify its effectiveness. The results obtained have been satisfactory, so the expectations raised by the client have been met.
Keywords: Burnishing, surface roughness, milling
Recibido / received: 24/06/2021. Aceptado / accepted: 28/10/2021.
(1) Departamento de Ingeniería Mecánica,Universitat Politècnica de Catalunya. Escola d’Enginyeria de Barcelona Est.
(2) Departamento de Ciencia e Ingeniería de Materiales,Universitat Politècnica de Catalunya. Escola d’Enginyeria de Barcelona Est.
Autor para correspondencia: Dr. J. Antonio Travieso-Rodriguez, e-mail: antonio.travieso@upc.edu
Introducción
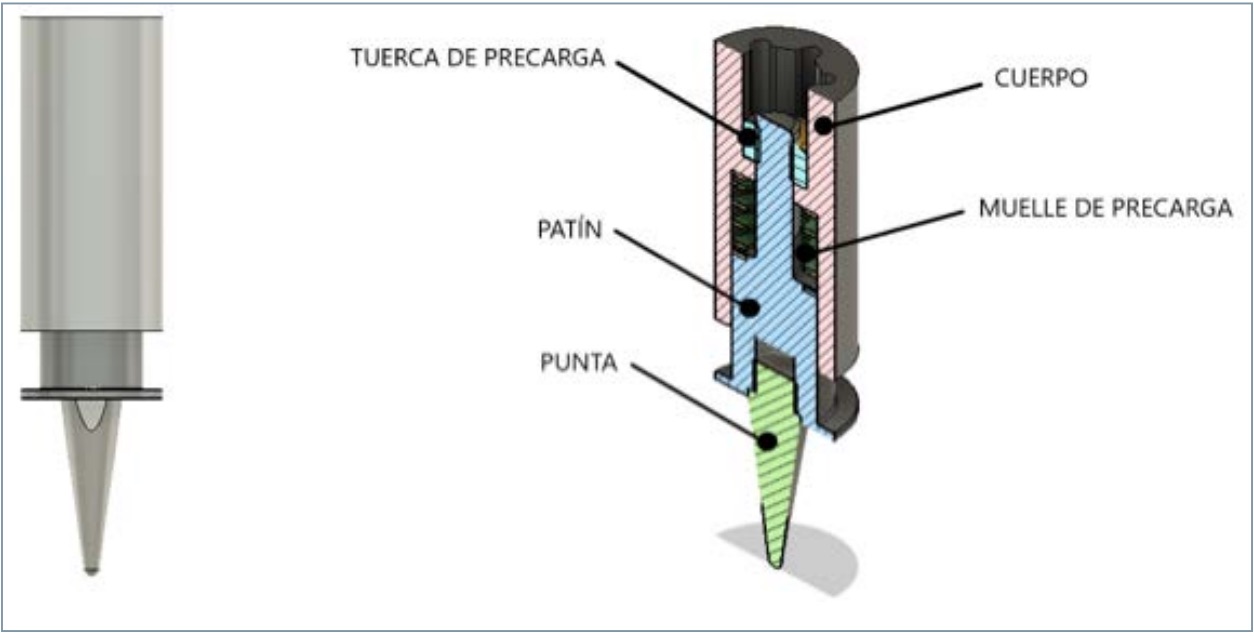
En la actualidad, la demanda de piezas en el sector de moldes y matrices viene acompañada de muchas exigencias por parte de los clientes, que buscan la máxima vida útil en estos componentes, sometidos a grandes esfuerzos y ciclos de fatiga debido a su uso continuado y a los requerimientos de productividad de las industrias como la automovilística, por ejemplo. Una de las características que más afecta al funcionamiento óptimo de las partes de un molde, que está en contacto con el material que se inyecta, es la calidad de su superfice [1, 2]. Cuanto menor sea la rugosidad superficial de esta superficie, mejor fluirá el material inyectado y, a su vez, las desgastará menos, con lo cual también tendrán más vida útil. Esto se traduce en tener un molde capaz de fabricar una mayor cantidad de piezas antes de ser desechado [3, 4]. Obtener una rugosidad a los niveles necesarios en este tipo de superficies complejas es un proceso muy trabajoso, que hoy en día en la mayoría de las factorías se hace a través de un proceso de pulido manual, con los inconvenientes que esto conlleva: consumen una gran cantidad de tiempo y requieren de mano de obra muy especializada, lo cual redunda en costes de fabricación muy elevados [5].
Uno de los procesos que se utiliza como alternativa al pulido manual es el bruñido. Los resultados de numerosos investigadores a lo largo de las últimas décadas han permitido confirmar sus efectos positivos la integridad de la superficie de piezas industriales, en tanto que se trata de un proceso mecánico capaz de mejorar simultáneamente la topología superficial, la dureza y las tensiones residuales de los materiales objetivo [6]. El proceso está basado en deformar plásticamente las irregularidades de la superficie objetivo mediante una punta que transmite una fuerza controlada, todo mediante la programación de rutinas de control numérico que permiten modificar el área de interés de la superficie objetivo [7]. Se puede realizar en diferentes tipos de piezas, tanto fijadas a un torno como a una fresadora [8, 9].
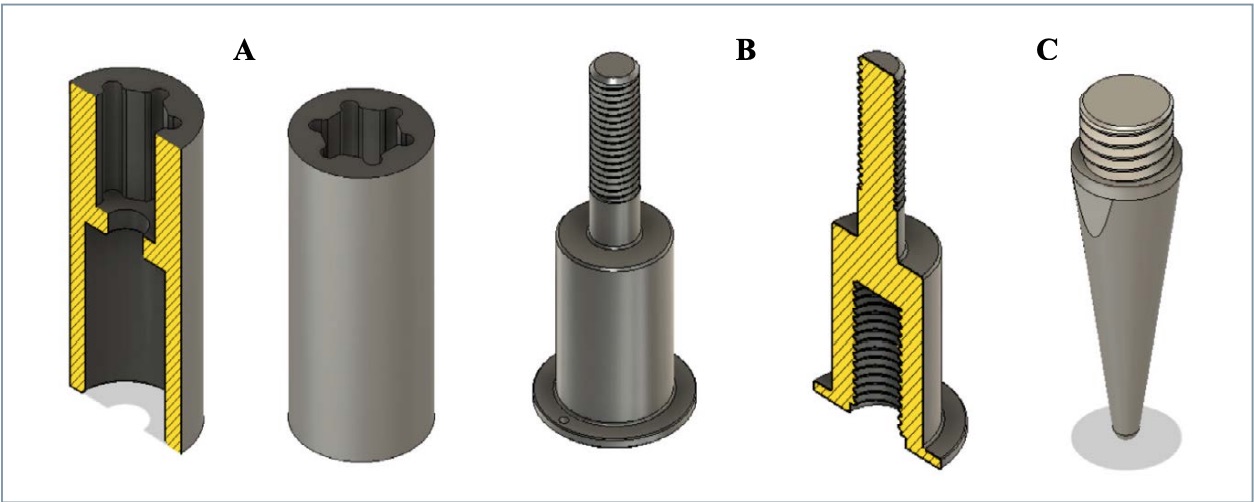
Este artículo tiene como objetivo presentar una nueva herramienta de bruñido de diseño y fabricación propia, patentada con la referencia P201931092 [10]. Esta herramienta tiene algunas características que la hace diferente de muchas existentes en el mercado. Las más utilizadas tienen una punta acabada en un elemento encargado de bruñir, en forma de bola o rodillo. Por ejemplo, Jerez Mesa et al. (2018) [11] desarrollaron una herramienta con punta de bruñir acabada en bola, para ser utilizada en un centro de mecanizado vertical. Mahajan & Tajane (2013) [12] desarrollaron otra también acababa en bola, pero para ser utilizada en torno. Otras casas comerciales, como Cogsdill Tool Products, Inc. [13] comercializa una herramienta acabada en un rodillo bruñidor que puede acabar únicamente superficies planas. En todos los casos expuestos, las herramientas están configuradas de forma que su diseño solo permite el tratamiento de superficies con características muy específicas, lo que disminuye su versatilidad. En todos los casos, el tratamiento de superficies cóncavas típicas de moldes está imposibilitado, sobre todo en máquinas fresadoras de 3 ejes.
El rasgo distintivo de la herramienta que se presenta en esta contribución es que la punta acaba en forma esférica, pero no es una bola que gira sobre sí misma. Esta forma de transmitir la fuerza de la herramienta permite el tratamiento de superficies cóncavas típicas de moldes. Sin embargo, el hecho de que la superficie esférica no ruede cambia completamente la forma en que se interactúa con el material bruñido, y demanda validaciones experimentales nuevas. La herramienta está diseñada de forma que las puntas esféricas son intercambiables, lo cual agilizaría el proceso de mantenimiento en una eventual aplicación industrial. De ahí que la novedad fundamental de este artículo es presentar esta herramienta y validarla a través de una aplicación experimental. Los resultados obtenidos, por otro lado, son de especial interés para la industria porque mediante este tipo de punta de bruñir se pueden llegar a tratar superficies que la mayoría de las herramientas que hay en el mercado no pueden, por su forma geométrica, sobre todo en máquinas de 3 ejes, por las limitaciones de movimiento que tienen las mismas. Por tanto, es una muy buena alternativa para el sector del molde y, sobre todo, en fábricas pequeñas que no disponen de muchas máquinas de más de 3 ejes, como la que solicitó la herramienta que se presenta.
Materiales y métodos
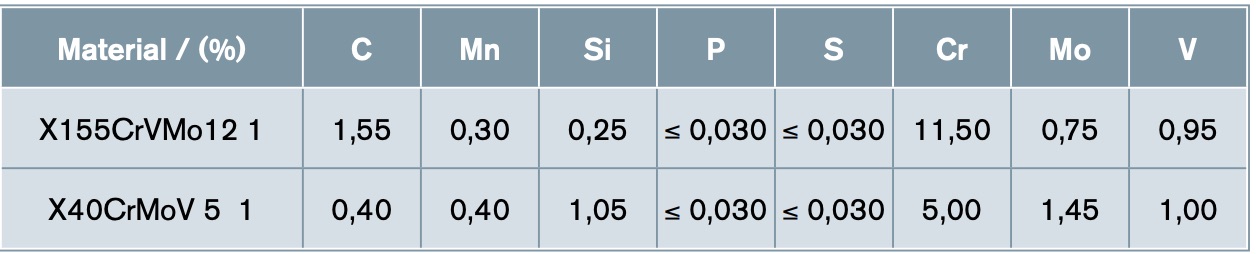
herramienta
Consideraciones sobre el diseño de la herramienta de bruñido
La herramienta ha sido diseñada con el fin de que sea capaz de bruñir las geometrías complejas de diferentes componentes de moldes de inyección. Está compuesta por un conjunto de cinco piezas, tres de las cuáles son de diseño propio y las dos restantes son piezas estandarizadas. En la figura 1 se puede ver la herramienta y sus diferentes partes.
El cuerpo (figura 2A) es el encargado de alojar el resto de los componentes principales de la herramienta como son el muelle de precarga, el patín y la tuerca de precarga. Al mismo tiempo, es la pieza que está en contacto con el portaherramientas que se monta en el centro de mecanizado. A la hora de diseñar la geometría donde se encuentra alojada la tuerca de precarga, se tuvo en cuenta que pudiera ser mecanizada sin tecnologías específicas como la electroerosión. Por esta razón, las esquinas del alojamiento hexagonal se encuentran perforadas a diámetro 4 milímetros.
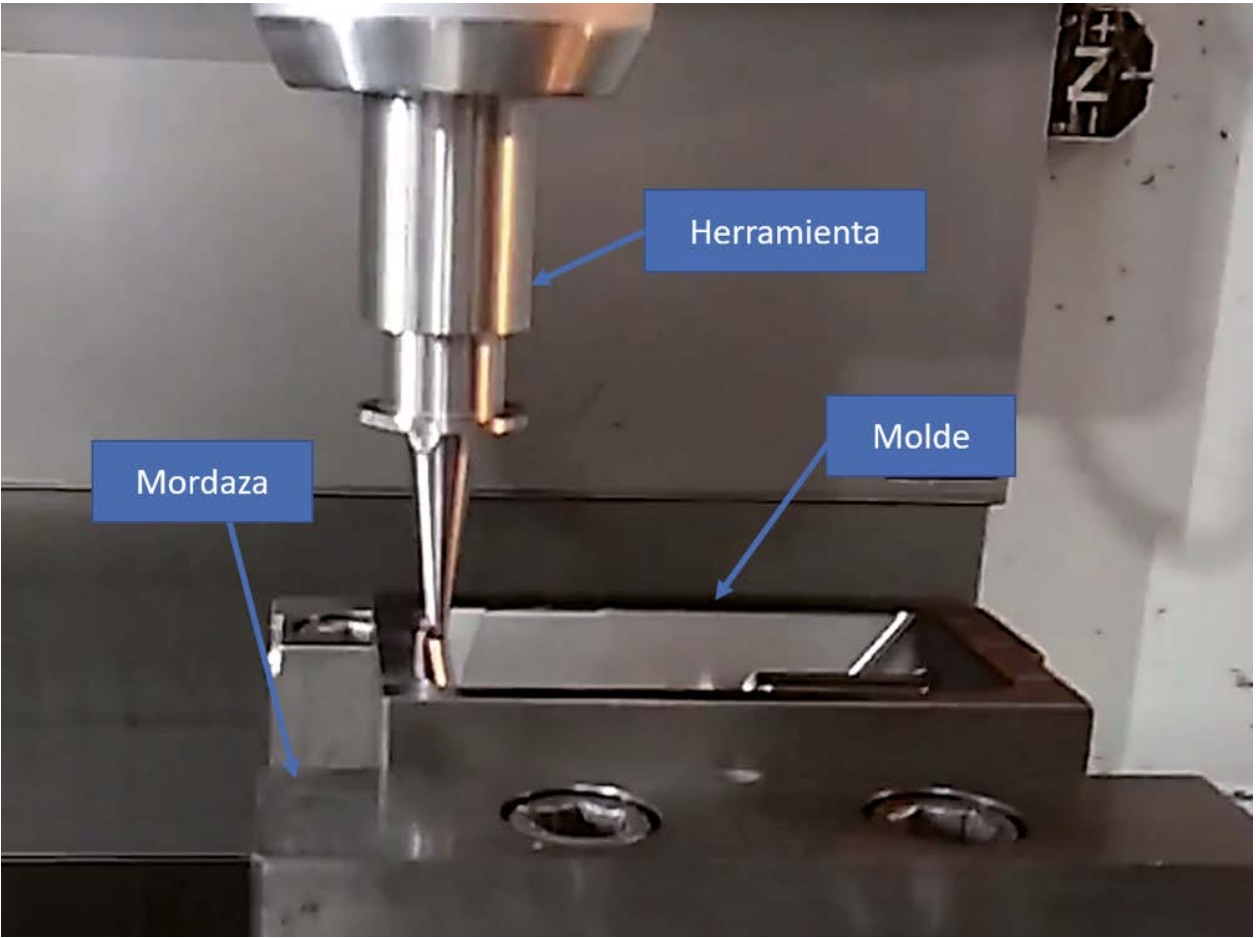
El patín (figura 2B) es el encargado de transmitir la fuerza elástica del muelle a la punta de bruñido. Va montado directamente en el cuerpo de la herramienta mediante un ajuste H7g6 para asegurar juego en todo momento y permitir el deslizamiento dentro de él. Está en contacto con el muelle de precarga y se une con la tuerca de precarga mediante una rosca M10x1. Este componente debe tener un juego ligero con la superficie interna del cuerpo para asegurar los desplazamientos en dirección axial, pero no radial a la hora de bruñir. Incorpora una rosca de tipo hembra en la que se montan las puntas de bruñido. Esto se debe a que, si ocurriera alguna colisión con otros elementos de la máquina o desgaste por uso, solo es necesario cambiar la punta. También permite el montaje de diversas geometrías y longitudes de puntas en la misma herramienta; simplemente se debe desmontar una y cambiarla por la otra.
La punta mostrada en la figura 2C tiene la función de transmitir la fuerza del patín a la pieza a la cual se le desea aplicar el superacabado. Hay diversas geometrías de puntas, las cuales se pueden cambiar en función de la pieza a bruñir. Todas ellas tienen en común que la punta que está en contacto con la superficie de trabajo es esférica. Incorpora en el extremo del montaje una rosca de M12x1,75 y una superficie de apriete para poderse montar y desmontar con la ayuda de una llave fija de 10 milímetros entre garras.
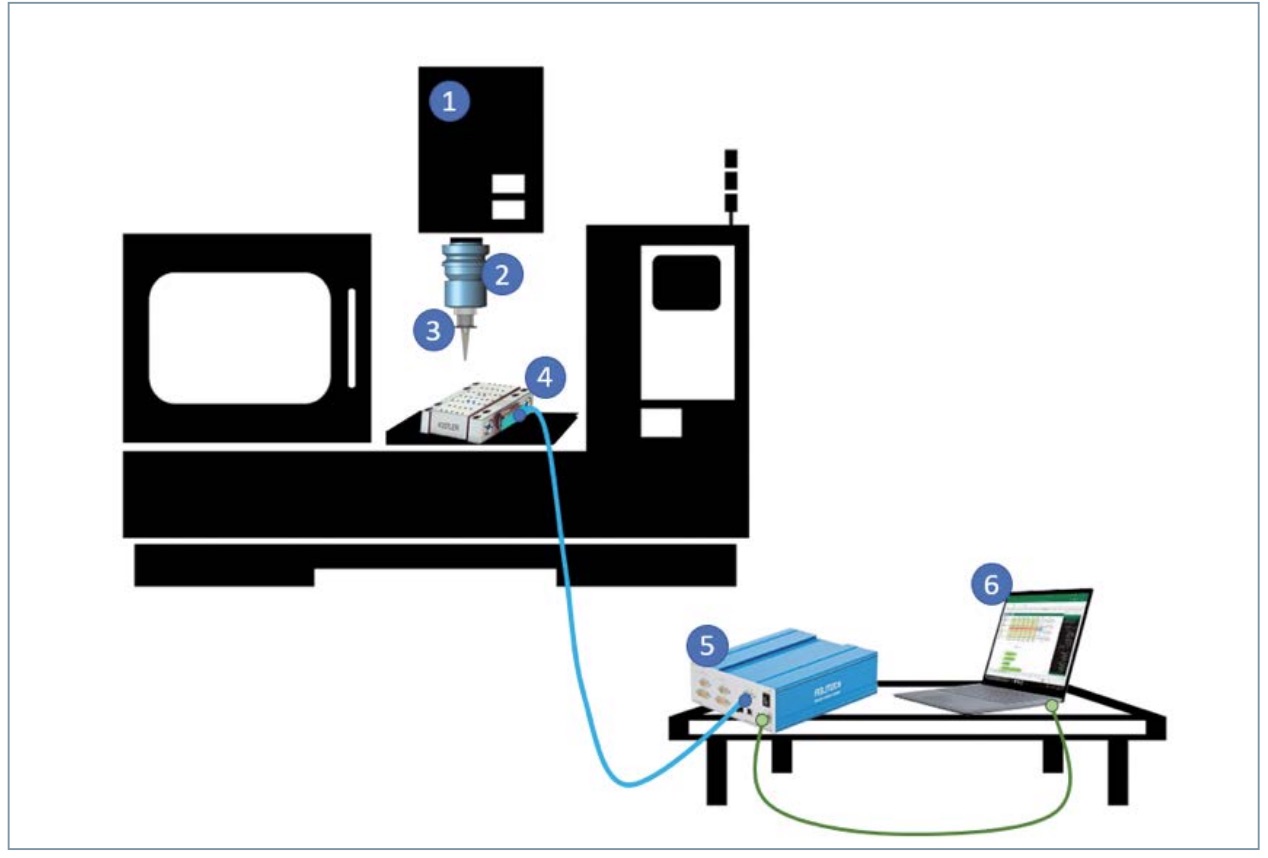
Por otro lado, también se necesitan dos elementos normalizados. En primer lugar, el muelle de precarga es el encargado de mantener la fuerza constante a medida que la herramienta va bruñendo la superficie de la pieza, de manera proporcional a su compresión como describe la ley de Hooke. Está unido al patín mediante un ajuste con juego, tanto con el patín como con el alojamiento interno del cuerpo de la herramienta. El muelle escogido para realizar las primeras pruebas de la herramienta ha sido un ISO 10243 cuya constante elástica es de 16 N/mm. Este muelle se puede comprimir la longitud suficiente como para llegar a realizar la fuerza necesaria para bruñir. Para el diseño propuesto, la carrera máxima de compresión posible combinada con la constante elástica anterior hace que la fuerza de bruñido máxima esté limitada a 240 N.
Por último, la tuerca encargada de precargar el muelle es el elemento normalizado DIN 980. Su función es mantener el patín unido al cuerpo y, al mismo tiempo, mantener la precarga inicial que se aplica al muelle. Se decidió que esta tuerca debía ser autoblocante para evitar posibles aflojamientos mientras la herramienta trabaja. Alojada en el agujero hexagonal del cuerpo, este se diseñó a partir de esta tuerca y para que se pudiera desplazar en la dirección axial pero no girar, y de manera que si ese movimiento no estaba restringido no se podía ajustar la precarga.
El montaje del sistema descrito dota a la herramienta de versatilidad, precisión y eficiencia, sin verse comprometida por ello su simplicidad. La guía debe permitir el movimiento axial entre los diferentes componentes para adaptarse a los cambios superficiales de las piezas, pero no debe tener un juego excesivo, ya que esto provocaría la pérdida de control del punto de contacto de la herramienta con la pieza.
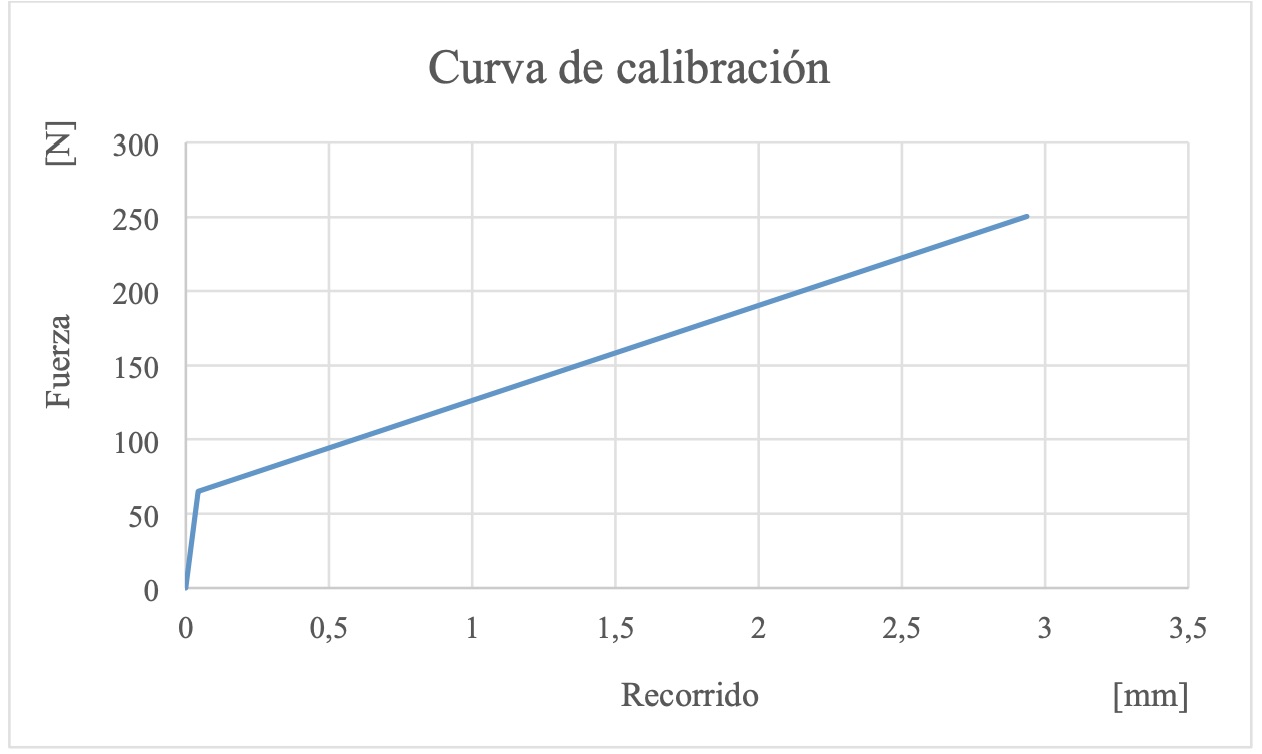
Materiales seleccionados para las diferentes partes de la herramienta
La herramienta de bruñido está sometida a elevados esfuerzos debido a su interacción con la pieza de trabajo y a los cambios de dirección durante su funcionamiento. La punta de la herramienta, sobre todo, está sometida a una fricción constante con el material a bruñir. Teniendo en cuenta las exigencias a las cuales puede ser sometida la herramienta, se estudiaron distintos materiales que pudieran soportar las exigentes condiciones de trabajo de la herramienta.
La punta de la herramienta está fabricada en acero X155CrVMo12 1. Este material se mecaniza en desbaste y luego se somete a un temple para conseguir una dureza superficial de hasta 60-62 HRC. Seguidamente, se rectifica para llevar la pieza a la medida final. La dureza conseguida es muy superior a la de las superficies de los moldes sobre las cuales trabaja, asegurando así una buena resistencia al desgaste. Este acero permite también diversos tratamientos superficiales como la nitruración y el physical vapor deposition (PVD), los cuales confieren un incremento de dureza superficial significativo (hasta 70-75 HRC), así como una mejoría en cuanto a la disminución de su coeficiente de fricción respecto al material de la pieza a bruñir.
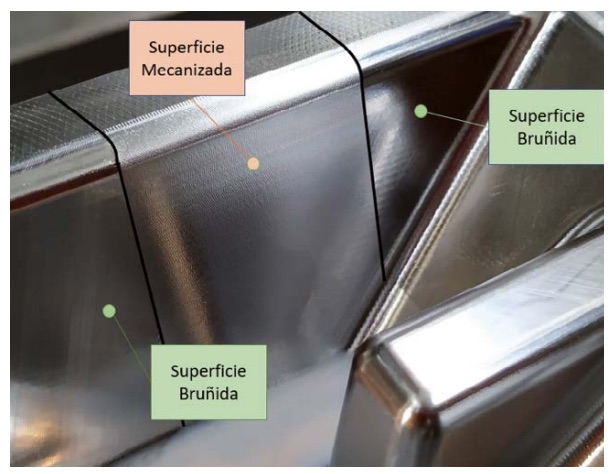
El material elegido para la fabricación del cuerpo y el patín de la herramienta ha sido acero X40CrMoV 5 1, con una dureza superficial media de 40-45 HRC. Este acero es utilizado para fabricar una gran cantidad de elementos mecánicos como portaherramientas para centros de mecanizado, diferentes componentes de moldes, etc. Esto se debe a su elevada resistencia mecánica, buena resistencia a la corrosión, elevada resistencia al desgaste y su buena maquinabilidad. Además, al fabricar ambos componentes con el mismo material, se puede asegurar que, pese a que haya cambios de temperatura, siempre se mantendrán las tolerancias de fabricación sin riesgo de que cambie el tipo de ajuste entre ellos. En la tabla 1, se muestra la composición química de ambos materiales.
Detalles sobre el proceso de fabricación de las diferentes partes de la herramienta
En primer lugar, se procedió a cortar el bruto del material para, posteriormente, ser torneado en un torno manual. La elección de la fabricación en torno manual se debe a que solo se fabricaron dos prototipos. Una vez torneadas se procedió a realizar el alojamiento del mecanismo de precarga en el cuerpo de la herramienta, el cual se realizó con un centro de mecanizado vertical AWEA AF1000. A las puntas se les realiza un tratamiento térmico de endurecimiento superficial para lograr dureza de 60- 62 HRC. Una vez templadas las puntas y mecanizadas el resto de las piezas de la herramienta, todas las superficies que lo requieran son rectificadas con una rectificadora cilíndrica CNC. En la figura 4, se puede ver una fotografía de la herramienta fabricada.
Calibración de la herramienta

Para poder comenzar a realizar los ensayos sobre piezas y poder determinar la efectividad de la herramienta se caracterizó la curva fuerza (desplazamiento del muelle a compresión). De esta forma, controlando la profundidad Z que penetra la herramienta en el programa de CN, se obtiene la fuerza de bruñido esperada. En la figura 5, se muestra la instalación montada para realizar la calibración de la herramienta. Para ello, se requirió de los siguientes elementos:
1. Centro de mecanizado vertical.
2. Portaherramientas hidráulico ISO40.
3. Prototipo fabricado de la herramienta.
4. Mesa de fuerzas KISTLER 9256.
5. Sistema de adquisición de datos KISTLER 5697ª.
6. Ordenador con Office365 y software de la mesa KISTLER DynoWare.
Una vez se dispuso de todos los elementos se procedió de la siguiente manera para extraer la curva en formato tabla y gráfico. Para ello, instalada la pieza en la mesa dinamométrica, se muestreó la fuerza a la que se llegaba en diferentes profundidades de penetración desde 0 hasta -15 mm. Esta rutina se llevó a cabo 5 veces para comprobar la repetibilidad de los resultados. La curva de calibración obtenida puede verse en la figura 6.
La herramienta tiene un comportamiento similar en los cinco ensayos realizados. Por tanto, se puede asegurar que la curva de calibración es suficientemente robusta. Una vez que se obtiene la curva de calibración se puede comenzar a realizar los ensayos combinando los diferentes parámetros de trabajo para probar la efectividad de la herramienta.
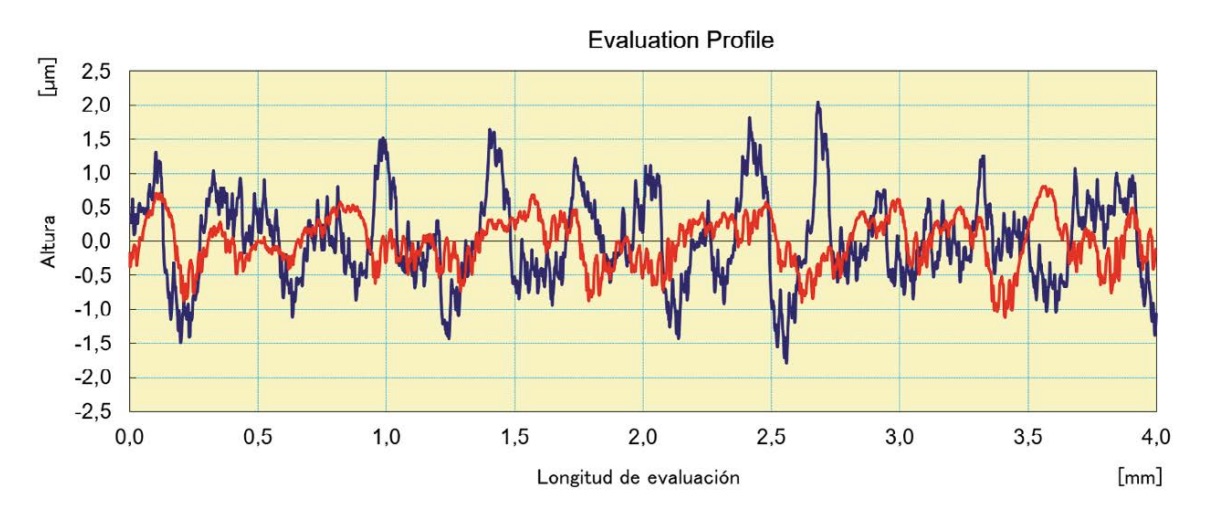
Ensayos experimentales de bruñido sobre el molde
Para comprobar que la herramienta fabricada está lista para su uso, se realizan diferentes ensayos sobre la superficie de un molde real, fabricado en acero X40CrMoV 5 1. Se bruñó una parte de la superficie total del molde, sobre una superficie previamente fresada con una fresa de bola de 6 mm de diámetro, cuatro labios de corte con velocidad de giro del cabezal de 10.000 min-1, una velocidad de avance de 220 mm/min, una profundidad de pasada radial de ae 0,1 mm y una profundidad de pasada ap de 0,1 mm (figura 7).
La superficie del molde se bruñó con una fuerza de 120 N, a 200 mm/min de velocidad de avance, con una pasada de bruñido y con un ancho de pasada lateral de 0,1 mm. Estos valores se tomaron teniendo en cuenta recomendaciones de experiencias anteriores.
Discusión de resultados
Con el fin de evaluar los resultados obtenidos en el experimento descrito anteriormente, se utilizará un equipo de adquisición de rugosidades 2D Mitutoyo SJ-210 para cada una de las superficies bruñidas, así como sobre la superficie fresada, con un cut-off de 0,8 mm. Se realizaron 10 mediciones para cada superficie con la finalidad de obtener una muestra estadísticamente sólida. Los parámetros de rugosidad superficial en cada una de las superficies medidas siguiendo la norma ISO4287:1999 han sido la rugosidad media aritmética, Ra y la media de los valores absolutos de los cinco picos más altos y valles más profundos del perfil dentro de la longitud de cut-off, Rz . Los valores medios de resultados de las mediciones de rugosidad, así como sus desviaciones típicas, se pueden observar en la tabla 2.
Los resultados de la tabla 2 se pueden observar mejor desde el punto de vista gráfico. En la figura 8, se puede ver gráficamente la comparativa entre la superficie fresada y la bruñida, con la consiguiente disminución de la escala del perfil.
Como se puede observar, en esta superficie se distinguen claramente los picos y los valles provocados por el fresado. Los parámetros característicos extraídos de este gráfico confirman los valores utilizados para realizar esta operación. Por ejemplo, la Ra de 0,472 ?m hace pensar que el avance por dientes utilizado es, aproximadamente, de 0,1 mm/rev. Estos valores son típicos de un proceso de fresado de acabado como el que se realiza en las superficies de un molde de inyección.
Los resultados de los parámetros de las huellas bruñidas mostrados en la tabla 2 demuestran que el bruñido disminuye considerablemente la rugosidad de esta superficie. La disminución de la Ra es del 29,6 % de media y la de Rz del 35,1 % de media.
La forma del perfil en este caso se ve bastante más aplanada. Esto es producto de la deformación que han sufrido los picos de las irregularidades de la superficie. El material que deforma la bola de bruñido es arrastrado e introducido en los valles del perfil. Por eso queda una superficie portante mucho más plana, que, además de tener una rugosidad más pequeña, ayuda a que fluya mejor el material que entra en contacto con ella, en el momento en que es inyectado dentro de la superficie del molde.
Conclusiones
Se ha diseñado, fabricado y probado una nueva herramienta de bruñido con ciertos elementos diferenciales respecto a la mayoría de las que hay en el mercado. Tras haber realizado distintas pruebas sobre un molde real, todas las soluciones constructivas han demostrado cumplir los requisitos fijados al inicio de la investigación. Se han conseguido bruñir superficies reales con valores de rugosidad adecuados a los que se solicitan en superficies de este tipo, siempre que se utilice la herramienta con la configuración adecuada. Por este motivo, y teniendo en cuenta que la herramienta es susceptible de ser integrada en procesos de mecanizado automatizados, puede concluirse que su potencial en el sector del mecanizado de moldes de inyección debe ser valorado y estudiado en profundidad en futuras acciones.
Financiación
Este estudio se pudo llevar a cabo gracias a la financiación del Ministerio de Ciencia, Innovación y Universidades de España, a través de la subvención RTI2018-101653-B-I00 y de la Generalitat de Cataluña y de fondos FEDER para el desarrollo regional a través de la subvención IU68-016744.
Referencias
[1] Zhang, H. L.; Ong, N. S.; Lam, Y. C. “Mold surface roughness effects on cavity filling of polymer melt in micro injection molding.” The International Journal of Advanced Manufacturing Technology, vol. 37, no 11-12, p. 1105-1112 (2008).
[2] Ding, Z., Zhao, J., Liu, H. y Dong, Y. “Effects of ball burnishing on surface properties of SKD11 mold steel.” Engineering Research Express, vol. 2, no. 2, pp. 025004 (2020).
[3] Martínez-Mateo, I., et al. “Surface damage of mold steel and its influence on surface roughness of injection molded plasticparts.” Wear, vol. 271, no 9-10, p. 2512-2516 (2011).
[4] Sachin, B.; Narendranath, S.; Chakradhar, D. “Sustainable diamond burnishing of 17-4 PH stainless steel for enhanced surface integrity and product performance by using a novel modified tool.” Materials Research Express, vol. 6, no 4, p. 046501 (2019).
[5] Fisher, Kenneth J., et al. Development of a cost model for manual tool polishing. The International Journal of Modern Engineering, vol. 6, no 2 ( 2006).
[6] Travieso-Rodríguez, J.A. et al., “Ball-burnishing process influence on hardness ans residual stresses of aluminium A92017” 17th International Research/Expert Conference ”Trends in the Development of Machinery and Associated Technology, Estambul (2013).
[7] Travieso-Rodríguez, Jose Antonio; Dessein, Gilles; González-Rojas, Hernan Alberto. “Improving the surface finish of concave and convex surfaces using a ball burnishing process”. Materials and Manufacturing Processes, vol. 26, no 12, p. 1494-1502 (2011).
[8] Hassan, Adel Mahmood. “The effects of ball-and roller-burnishing on the surface roughness and hardness of some non-ferrous metals”. Journal of materials processing technology, vol. 72, no 3, p. 385-391 (1997).
[9] Salahshoor, M., et al. “Surface integrity and corrosion performance of biomedical magnesium-calcium alloy processed by hybrid dry cutting-finish burnishing”. Journal of the mechanical behavior of biomedical materials, vol. 78, p. 246-253 (2018).
[10] Patente española P201931092, presentada a la OEPM el 10 de diciembre de 2019.
[11] Jerez-Mesa, Ramón; Gomez-Gras, Giovanni; Travieso-Rodriguez, Jose Antonio. “Surface roughness assessment after different strategy patterns of ultrasonic ball burnishing”. Procedia Manufacturing, vol. 13, p. 710-717 (2017).
[12] Mahajan, Deepak; Tajane, Ravindra. “A review on ball burnishing process”. International Journal of Scientific and Research Publications, vol. 3, no 4, p. 1-8 (2013).
[13] https://cogsdill.co.uk/products/burnishingtools/diamond-burnish-face-mill-tools/, consultada por última vez el 9 de mayo de 2020.